Home
Ultrasonic Cleaner
High frequency desktop ultrasonic Cleaner
High frequency desktop ultrasonic Cleaner BULC-505



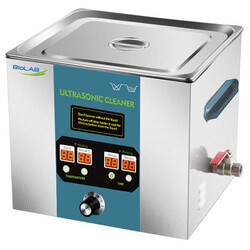
High frequency desktop ultrasonic Cleaner BULC-505
- Sea, Air, Door to Door Shipping
- 1 Year Warranty
- US & European Standards
High frequency ultrasonic cleaner is mainly used in medical industry, computers, microelectronics computers. It uses high frequency to clean the sub micron dirt without damaging the equipment
- Digital display and control ultrasonic power adjustable range from 0 to 100%
- Special high frequency ultrasonic transducer (53/68/80/100/132 Khz)
- No stud- welding technology, Cleaning effect is better
- MCU SWEEP multi frequency ultrasonic generator output, frequency sweep drive ultrasonic cleaning effect more powerful
Specification
Features
Capacity | 11 L |
Working frequency | 53/68/80/100/132 Khz |
Ultrasonic Power | 240 W |
Heating power | 300 W |
Timing time | 1- 99 mins |
Temperature range | 0- 80℃ |
Power regulation | 0-100 % |
Drain valve | Yes |
Washing basket | Optional |
Inner tank dimension | 300x240x150 mm |
Packing size | 300x240x150 mm |
Gross weight | 8.5 kg |
Power Supply | 220V+ 10% 50Hz/60Hz 110V+ 10% 50Hz/60Hz |
- Digital display and control ultrasonic power adjustable range from 0 to 100%
- Special high frequency ultrasonic transducer (53/68/80/100/132 Khz)
- No stud- welding technology, Cleaning effect is better
- MCU SWEEP multi frequency ultrasonic generator output, frequency sweep drive ultrasonic cleaning effect more powerful
- MHC heating system, maximum temperature is up to 80℃
- All stainless steel material inner tank is made by punching SUS304 1.0mm
- 2500V high voltage test to ensure the product safety, strict production, aging production quality control
Operating Manual for BULC-505

1. Packing List
2. Principle of ultrasonic cleaning
3. Product Features
4. Technical Parameters
5. Scope of Application
6. Installation and Preparation
7. Operation Instructions
8. Factors Influencing Performance
9. Maintenance
10. Malfunctions and Solutions
11. Application Safety
12. Warranty
Warranty will be invalid in any one of the following cases:
1. Packing List
Item | Quantity | Accessories | Quantity |
Ultrasonic cleaner | 1 | Cover | 1 |
Operation manual | 1 | Power cable | 1 |
Washing basket | 1 (optional) |
Table 1
Please confirm whether the above items are complete and intact. If there is any damage or lack of accessories, please contact the dealer.
2. Principle of ultrasonic cleaning
Ultrasonic cleaning machine generates ultrasonic frequency electricity, which is converted by energy converter into high-frequency mechanical oscillation that is transferred to cleaning fluid. Ultrasound wave is beamed forwards unevenly in the cleaning fluid to make the fluid vibrate and generate tens of thousand of micro bubbles, which form and grow in the negative pressure area where the ultrasound wave travels longitudinally and close (crush out) in positive pressure area. Formation, growth and quick closure of the micro bubbles is called cavitation. In cavitation, closure of bubbles will generate instantaneous high pressure higher than 1,000 times of atmospheric pressure, and the continuous high pressure force hits surface of the work piece like numerous small blasts to peel off dirty on the surface and in clearance of object, and this is how the ultrasonic cleaning machine operates.3. Product Features
1. Proprietary MCU-sweep ultrasonic wave generator driver circuit to present uniform and strong cleaning performance and to minimize noise level.2. Proprietary industrial ultrasonic transducer with high Q value and energy conversion efficiency at stable output.
3. Imported high-strength adhesive, staple-free bonding, and long service life of tank
4. Digital timing for heating control between 1-99 minute and temperature setting between 1-80℃.
5. Internal tank fabricated of 1.0mm SUS304 stainless steel to present good performance and long service life.
6. Cleaning basket made of 304 stainless steel and electro-polished.
7. Outer shell made of high-quality stainless steel to present good corrosion resistance.
4. Technical Parameters
Model | Internal Dimensions (L*W*H) | External Dimensions (L*W*H) | Volume (L) | Gross Weigh t(KG) | Ultras onic Power (W) | Drain valve | Heating Power( W)) | Frequ ency( KHz) | Time( Min) | Heating Tempera ture(℃) |
BULC-505 | 300*240*150 | 368*270*290 | 11 | 8.5 | 240 | no | 300 | 53/68/80/100/120/130(option all) | 1-99 | 1~80 |
Table 2
5. Scope of Application
Industry | Describe |
Instrumentation | Cleaning of measuring tools and fine cleaning of precision parts prior to assembly |
Electronics | Removal of rosin and welding spots on printing circuit board and cleaning of HV contacts and other electronic parts. |
Medical care | Cleaning, disinfection and sterilization of medical devices and lab glassware. |
Semiconductor | Fine cleaning of semiconductor chips. |
Timepiece and jewelry | Removal of grease, dirt, scale and polishing paste. |
Chemicals and biologicals | Cleaning of lab glassware. |
Optics | Cleaning of optical components and lens. |
Textile dyeing and finishing | Cleaning of spinning spindle and spinneret. |
Petrochemicals | Cleaning of metal filter mesh, chemical containers and exchanger. |
Surface treatment | Removal of oil and rust before galvanic coating, cleaning and phosphating process before ion plating, removal of accumulated carbon, scale and polishing paste, activation of surface of work piece. |
Machinery | Removal of oil/grease on parts and components, cleaning of engine, carburetor and automobile parts and components, filter, and filter mesh. |
Table 3
6. Installation and Preparation
1. Place the machine horizontally at a well-ventilated and dry location.2. Select appropriate detergent, cleaning water or other solution based on properties of work piece to be cleaned.
3. Properly and firmly connect the plug to a three-pin power socket which is grounded reliably to ensure safety.
7. Operation Instructions
Picture of Product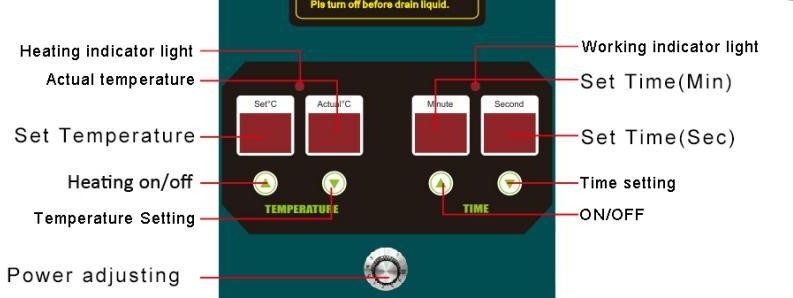
Figure 1
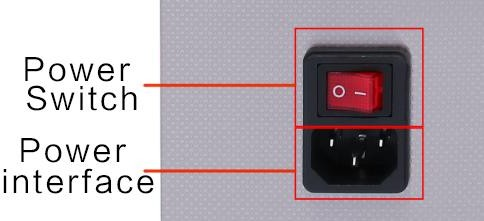
Figure 2
Operation Instructions:
1. Load cleaning fluid into the tank and connect the power supply (which shall be grounded reliably). After power-on, current actual temperature is displayed and the default temperature is 20℃. The ultrasound wave operating time is 99 minutes by default.
2. Adjustment of ultrasound wave operating duration: Press time setting button, one push
to increase one minute; long press it to increase fast, in a loop of 1-99 minutes.
3. Adjustment of operating temperature: Press temperature setting button, one push to increase one degree; long press it to increase fast, in a loop of 1-80 degree.
4. After target temperature is set properly, press heating on/off button to start heating tank (heating system is started and heating indicator lamp turns on when target temperature is higher than current actual temperature; heating system is stopped when target temperature is lower than current actual temperature), and press it again to stop heating.
5. After operating duration is set properly, press time on/off button to start operation and the operating indicator lamp turns on; press the button again to stop operation and operating indicator lamp goes out.
6. Power adjusting knob: Turn it clockwise to increase ultrasonic wave cleaning power or counterclockwise to reduce cleaning power (this function is unavailable in 8120/8180L
/8240Lmodel).
8. Factors Influencing Performance
1. Ultrasonic power density:Higher power density results in better cleaning performance and higher cleaning speed. Higher power density is appropriate for cleaning of work piece with stubborn dirt, and lower power density is suitable for any precision work piece (generally ultrasonic power density ranges between 0.01-0.02w/ml).2. Ultrasonic Frequency: Lower frequency results in better cavitation performance. Higher
frequency contributes to better refraction/ reflection performance. Lower frequency should be applied for cleaning of simple surface while higher frequency for cleaning of complex surface with deep or inaccessible hole. (80KHz, 120KHz)
3. Cleaning temperature: Ultrasound wave will present the best cavitation performance at a temperature range between 40~50℃.Higher cleaning temperature facilitates breakdown of dirt, while a temperature above 70℃~80℃ may impair effect of ultrasound wave and deteriorate cleaning performance.
4. Cleaning duration:Longer cleaning duration presents better cleaning performance (except for special material).
5. Other influential factors include type and properties of cleaning fluid and the dirt to be removed.
9. Maintenance
This machine shall be used, maintained by dedicated personnel and a full check on the equipment shall be performed regularly.1. Check the power supply and line connections for any looseness, overheating, damp absorption or poor contact.
2. Inspect sealing of the bottom board of cleaning tank for any leakage.Check the joint between drain pipe and cleaning tank for leakage.
3. For looseness of ultrasound wave converter or burnout of power tube, contact the manufacturer immediately.
4. The ultrasound wave equipment shall be operated and stored at well-ventilated, dry and clean place to facilitate good performance and long service life.
10. Malfunctions and Solutions
malfunctions | solutions |
Failure of Ultrasonic Wave | Check whether the power cable has been connected properly (by inspecting operation of power indicator lamp). Check whether PCB has been connected properly to the power socket. Check whether the fuse tube is broken |
Weak ultrasonic wave | Check whether the power voltage is normal. Inspect whether the energy converter get loose or there is any shock absorption material or work piece under the tank. Check whether cleaning fluid temperature is normal (recommended operating temperature is higher than 30 degree) or there are many air bubbles in the fluid or on the tank wall (repeated power-on/off will reduce the bubbles). Check whether the solvent is added excessively. |
No heating | Check whether target temperature is too lower (lower than current actual temperature). Check whether the heater cable is disconnected or gets loose. Check whether heater is broken (due to shortage of cleaning fluid) |
Electric leakage | Check whether the machine has absorbed damp or corroded. Check whether cable tray to each component is damaged, loosened or broken. Check whether the earthing wire is in good condition. |
Table 4
11. Application Safety
Safety Considerations:1. Warns: This product contain dangerous voltage, so do not start it at a high-temperature or humid location to avoid electric shock.
2. Do not impose great impact to this machine, and handle it with care to prevent impairment to performance or life span of it.
3. Locate this machine properly to avoid any accident resulted from children's access to it.
4. Perform any maintenance operation only after the power supply is disconnected to avoid any safety accident.
5. The machine contain high voltage during operation, so do not dismantle its enclosure to avoid any hazard.
6. For any damage to the power cable, contact your service center or your dealer for replacement.
7. Clean the enclosure with soft dry cloth after disconnecting the power cable.
8. Protect the machine from splash of rain or water to avoid electric shock or fire, and keep it away from any location with high temperature or humidity.
9. For reason of personal safety, do not dismantle the enclosure for repair or change on your own.
Safety Considerations:
1. During normal operation of ultrasonic generator, a consistent sound is resulted from the harmonic oscillation of the tank body impacted by ultrasound wave, and no agitation but ripple is caused on the surface of cleaning fluid by explosion of cavity. In case of discontinuous oscillation, increase or reduce the cleaning fluid by a small quantity to eliminate such oscillation to facilitate cleaning of work piece.
2. While ensuring adequate cleaning of work piece, keep the generator operating intermittently, as long-term consecutive operation may result in high temperature insides and accelerate aging of electronic components in it.
3. Absolutely do not use any inflammable detergent.
4. Start heating or ultrasonic wave generator only when the cleaning tank contains fluid, or otherwise the machine may be burnt out or even result in fire.
5. Prevent splash of cleaning fluid or water into the machine or energy converter, which may cause electric leakage or short circuiting, and thereby damage to the converter.
6. Any foreign matter falling into the tank shall be taken out immediately.
7. Before changing or discharging the cleaning fluid, make sure the fluid is at normal temperature and the ultrasonic wave generator is shut down and the power supply is disconnected.
8. Remove any dirt in the tank after operation.
9. Keep the external surface of the machine clean.
12. Warranty
1. Validity of warranty: One year from the date of purchase2. Please keep this after-sale service card properly, or otherwise the warranty will be invalid.
Warranty will be invalid in any one of the following cases:
◦ The machine fails or is damaged due to improper use or unauthorized disassembly of the product by user.◦ The machine is damaged due to force majeure (e.g. fire, flood, earthquake).
◦ The machine is damaged due to failure to operate the machine in accordance with the instructions.
◦ The machine is damaged due to improper repair by anyone other than our technician.
◦ The warranty card and/or purchase invoice is unavailable or be altered without authorization.
Warranty Card | |||
User Information | |||
Customer Name | User's Telephone | ||
User's Address | |||
Product Information | |||
Product Model | Attached Number | ||
Purchase Date | Dealer Name | ||
Dealer's Telephone | Dealer's Seal | ||
Dealer's Address | |||
__________________ | _________________ |