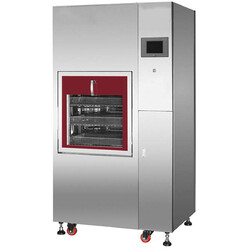
Glassware Washer BGLW-202
- Sea, Air, Door to Door Shipping
- 1 Year Warranty
- US & European Standards
Medical Automatic glassware provides standard and automatic cleaning and disinfection for most of medical equipment, so as to eliminate the possibility of infection in cleaning and disinfecting. It includes washing, disinfection and drying of various laboratory equipment such as flasks, beakers, pipettes and so on
- Two toughened glass doors,prevent cross infection
- Color LCD touch screen, advanced progammable control system with six standard programs
- High efficient cleaning system, with rotary nozzles in top,bottom and among the shelves to make sure that the spray liquid can contact the surface of devices completely
- High efficient drying system with HEPA filter, can clean and dry the inner of tubular things
Specification
Features
Applications
Capacity | 320 L |
Water Consumption Cycle | 24 L |
Inlet Water Pressure | 0.03~0.8 Mpa |
Noise | < 60 dB |
Material | Stainless Steel |
Overall Power Consumption | 17 KW |
Power Consumption- Water Washing | 1.5 KW |
Power Consumption- Water Heating | 15 KW |
Power Consumption-Drying | 3.6 KW |
Power Supply | 380 V , 50 Hz (Standard) ,110 V , 60 Hz (Optional) |
Standard Cleaning Rack | BK01-320x1 (5 layers) |
Standard Accessories | Built-in printer, One Bucket RBS A 156 leaner (1 L), One bucket RBS A 375 nuetralizer (1 L) |
Optical Accessories | Trolly (BKO 1) |
Washer Chamber Size (WxDxH) | 600x629x820 mm |
External Size (WxDxH) | 960x800x2030 mm |
Package Size (WxDxH) | 1200x1000x2350 mm |
Gross Weight | 370 kg |
- Two toughened glass doors,prevent cross infection
- Color LCD touch screen, advanced progammable control system with six standard programs
- High efficient cleaning system, with rotary nozzles in top,bottom and among the shelves to make sure that the spray liquid can contact the surface of devices completely
- High efficient drying system with HEPA filter, can clean and dry the inner of tubular things
- Thermal disinfection, water heating system can make sure the water temperature keep above 93°C to reach the international disinfecting efficiency level.
Medical, Pharmaceutical, Research institutes, Chemical industry, Microbiology Lab, University
Operating Manual for BGLW-202

I. Summary
1. Product Introduction
2. Product Parameter
II. Installation
1. Safety Criterion
2. InstallationCondition
3. Installation
III. Operation
4. Manual test
5. Operating system
6. Password protection
7. Single program
IV. Abnormal Conditions Treatment
1. Abnormal conditions treatment
2. Others abnormal situations
3. Failure alarming reset
V. Service And Maintenance
1. Regular Maintenance
2. Function Inspection
VI. Transportation
VII. Appendix
1. Washer disinfector placing diagram
2. Ventilation & drainage installation diagram
3. A0 value display
4. Liquid Agent Add
VIII. Packing List
I. Summary
1. Product Introduction
This machine is one full automatic machine for washing, disinfection and drying process.It is suitable for pharmaceutical companies, research institutions, university Laboratory customers to wash the laboratory glassware such as flasks, beakers, pipette, Petridishes, wide mouth bottle,etc.2. Product Parameter
Model | BGLW-202 |
Capacity(L) | 320 |
Voltage(V/HZ) | 220/50 |
Power(kW) | 6 |
ExteriorDimension(L×W×H)(mm) | 940*700*2020 |
WaterTemperature(℃) | RT~93 |
Power of Water heater(kW) | 5 |
Power of Dryer(kW) | 3 |
Water(L/circle) | 22 |
Noise(dB) | ≤55 |
LayerofRacks(layer) | 5 |
II. Installation
1. Safety Criterion
• Before the Installation,service and using the machine,please read operation manual carefully.
• The machine should be service by professional engineer as per the operation manual.
2. InstallationCondition
No. | Items | Requirement |
1 | Environment Requirement | •Ambient Temperature:4℃~45℃. •Ambient Humidity:≤80%. •Environment Requirement:The machine should avoid to be used in dust,shock and outdoor environment. |
2 | Headwaters Requirement | •Inlet Water Pressure:0.03~0.8Mpa. •Water Quality:Pure Water, Softened water,or distilled water. |
3 | Power Requirement | •Voltage:220V/50Hz |
Notes:The User should install another booster pump to improve the inlet water pressure if the inlet water pressure is too low.
3. Installation
3.1 In position
1) Dismount out package,read this manual carefully,check according to the contents in packing list if Accessories are complete and are in good condition.2) Move equipment to the installing site,adjust foundation level and make instrument in level position.
3) If equipment is put against walls,the nit stop should atleast be 50 mm away from the wall,and its sides should keep a distance of more than 20 mm away from walls.
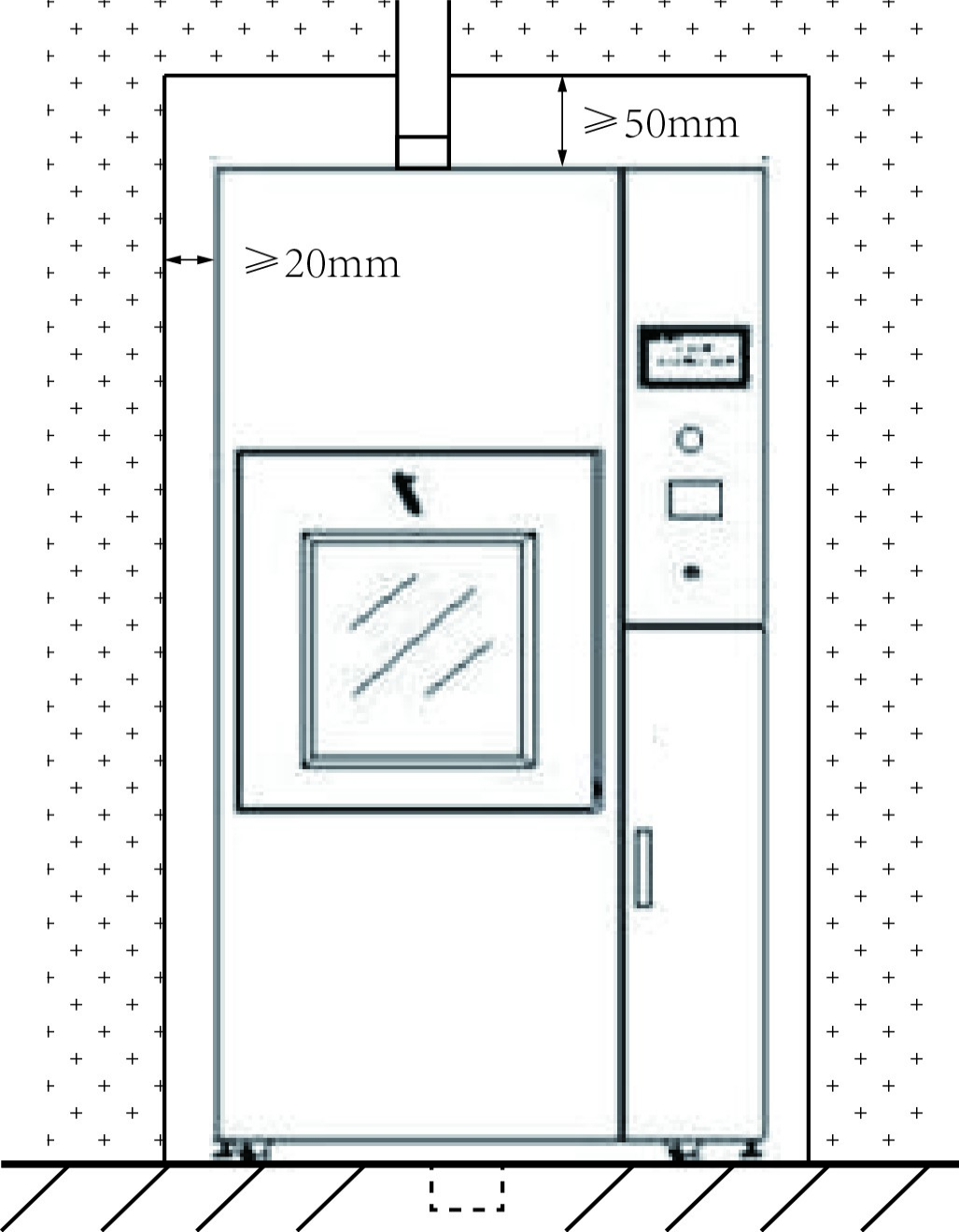
4) If several machines are installed in series,all machines should be adjusted to a same level.
5) Check if washing racks are put in order.
6) Check installation environment,it will be not suitable for installation in the following conditions.
• With heavy dust,oil stain,or conducting particles,corrosive gas,or flammable gas.
• With high temperature,high humidity,or is easy to get wringing.
• With Strong Magnetic Field.
3.2 Electric Connection
1) Power switch box is installed on the wall that is not far from instrument and is easy for operator to work;electricity leakage protector must be installed switchbox.
2) Please make sure that safety of body and equipment is guaranteed,one earth cable must be applied.
3) Power:AC 220V/50Hz.
4) Main Power Connection Diagram.
Instruction:
• The separate circuit breaker is required for machine installation,the circuit breaker should be 60A/220V
• The power line connection must be as per the label on the wiring harness
• The main power line is 2.5 meter
• The power phase sequence may be not match with the wiring phase sequence of the machine.
Open the frontboard to check the circulation pump running direction,and adjust the wiring phase sequence if required.
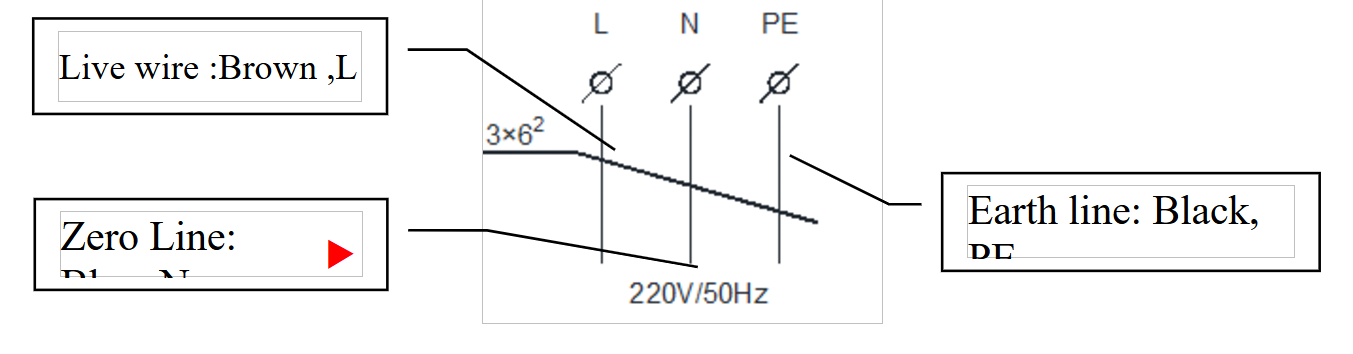
![]() | The power connection must be reliable at earth potential. |
The main power connection should be done by professional electric engineer. |
3.3 Water connection
1) The fast coupling is supplied together with the machine,the interface between inlet water pipe and water source pipe is standard DN25 fast coupling.
2)Open the water inlet valve after the pipe connection,visual inspection for the connection point of the water pipe,confirm no water leakage phenomenon.
3.4 Drainage Installation
Floor drain must be lower than the surface of the ground(drainage pipe lower than the machine),put the drainage pipe into the floor drain directly.
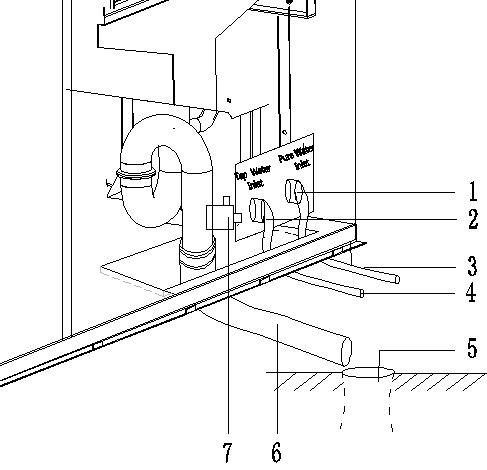
NO. | Parts | NO. | Parts |
1 | Pure Water Valve | 2 | Tap Water Valve |
3 | Purified Water Pipe | 4 | Tap Water Pipe |
5 | The Floor Drain | 6 | Drainpipe |
III. Operation
1. General view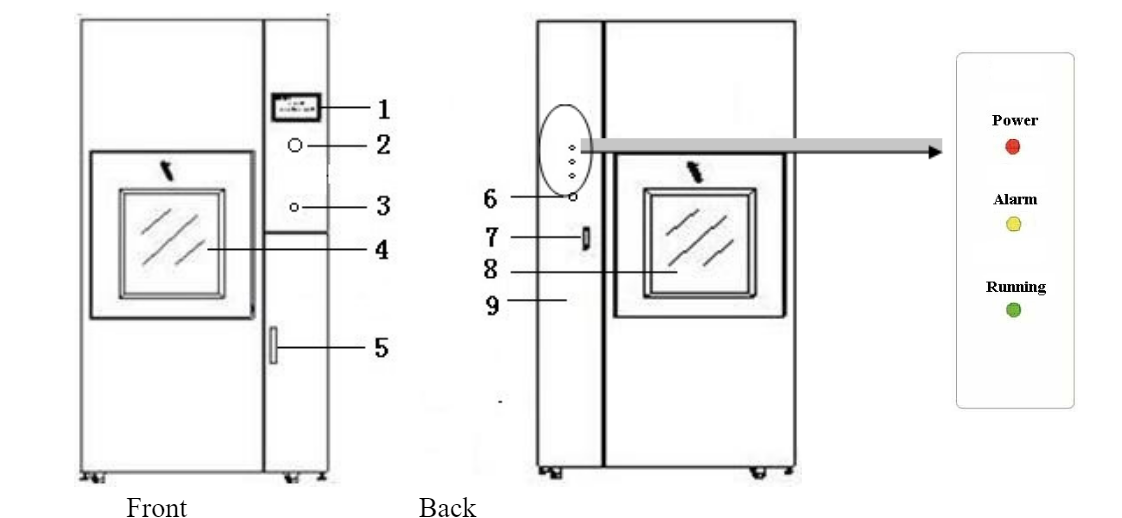
1-Touchscreen
2-Emergency Stop Button
3-Front Door Lock Button
4-Frontwatchwindow,
5-Doorknob
6-Backdoor Lock Button
7-Doorknob
8-Back watch window
Structures
The washer disinfector mainly consists of cleaning room,cleaning carriage,pipe,double doors,controlling system and drying system.
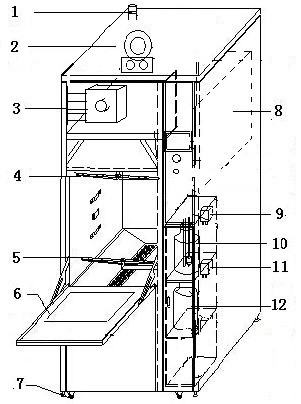
1- GasVent
2- Drying Fan
3- Air Filter
4- Top Spray Arm
5- Bottom Spray Arm
6- Frontdoor
7- Universal Wheel
8- Controlbox
9- EnzymePeristalticpump,
10- Enzyme Barrel,
11- Lubricant Peristalsis Pump
12- Lubricant Barrel
2. Operation
Load instruments to be cleaned on to the cleaning carriage and send it into the machine.
• Make sure that cleaning arm scan turn around flexibly without touching instruments.
• Select programs in the following way:
-After turning on the machine, select“Start mainpower”.Power-on interface will be shown on the touching screen of pollution area and meanwhile the red powerlight of clean area will be on.
-Select one from the 6 preset programs shown on the screen according to your needs.(About program setting please see appendix)
-Press“Start”to begin the program.
• When the program is running, process will be show non the touching screen,including the stage name, temperature, running time and soon.The green indication light of clean area will be on and the operation stages will be shown on touching screen.
• When the program is finished,the touching screen will show“program finished”and door at the clean side will be unlocked.
![]() | If the article has not cooled after being processed,take care of not being burned. |
• Take the cleaning carriage as well as accessories out of the cleaning room and then close the door at the cleanside.
• For the same program,just press“Start”once more.
• If the program has to be stopped during the operation process,press“Stop”on the screen and the door of pollution area can be opened.
3.Program
1) Programs list
program | Instruments Applicable | Procedures | Time(min) | Temp(℃) | Dose (ml) | Water |
1 | Surgical Instrument | Enzyme Washing(S) | 5 | 40 | 180 | Softwater |
1stRinsing(S) | 2 | / | / | Softwater | ||
2ndRinsing(RO) | 2 | / | / | ROwater | ||
Disinfection | 3 | 93 | 150 | ROwater | ||
Drying | 15 | 60 | / | |||
2 | Anesthesia Instrument | Enzyme Washing(S) | 5 | 40 | 180 | Softwater |
1stRinsing(S) | 3 | / | / | Softwater | ||
2ndRinsing(RO) | 3 | / | / | ROwater | ||
Disinfection | 3 | 93 | 150 | ROwater | ||
Drying | 15 | 60 | / | |||
3 | Bowl | Enzyme Washing(S) | 5 | 40 | 160 | Softwater |
1stRinsing(S) | 2 | / | / | Softwater | ||
2ndRinsing(RO) | 2 | / | / | ROwater | ||
Disinfection | 3 | 93 | 150 | ROwater | ||
Drying | 15 | 60 | / | |||
4 | Slippers | Enzyme Washing(S) | 6 | 40 | 170 | Softwater |
1stRinsing(S) | 3 | / | / | Softwater | ||
2ndRinsing(RO) | 3 | / | / | ROwater | ||
Disinfection | 3 | 93 | 150 | ROwater | ||
Drying | 15 | 60 | / | |||
5 | ToiletBasin | Enzyme Washing(S) | 8 | 40 | 180 | Softwater |
1stRinsing(S) | 2 | / | / | Softwater | ||
2ndRinsing(RO) | 2 | / | / | ROwater | ||
Disinfection | 3 | 93 | 150 | ROwater | ||
Drying | 15 | 60 | / | |||
6 | Breathing Duct | Enzyme Washing(S) | 10 | 40 | 180 | Softwater |
1stRinsing(S) | 2 | / | / | Softwater | ||
2ndRinsing(RO) | 2 | / | / | ROwater | ||
Disinfection | 3 | 93 | 160 | ROwater | ||
Drying | 15 | 60 | / | |||
7 | Minimally Invasive Instrument | Enzyme Washing(S) | 8 | 40 | 180 | Softwater |
1stRinsing(S) | 3 | / | / | Softwater | ||
2ndRinsing(RO) | 3 | / | / | ROwater | ||
Disinfection | 3 | 93 | 160 | ROwater | ||
Drying | 15 | 60 | / | |||
8 | Humidifying Bottle | Enzyme Washing(S) | 10 | 40 | 180 | Softwater |
1stRinsing(S) | 3 | / | / | Softwater | ||
2ndRinsing(RO) | 3 | / | / | ROwater | ||
Disinfection | 3 | 93 | 150 | ROwater | ||
Drying | 15 | 60 | / | |||
9 | Dental Handpiece | Enzyme Washing(S) | 6 | 40 | 180 | Softwater |
1stRinsing(S) | 3 | / | / | Softwater | ||
2ndRinsing(RO) | 3 | / | / | ROwater | ||
Disinfection | 3 | 93 | 150 | ROwater | ||
Drying | 15 | 60 | / | |||
10 | TestTube | Enzyme Washing(S) | 10 | 40 | 180 | Softwater |
1stRinsing(S) | 3 | / | / | Softwater | ||
2ndRinsing(RO) | 3 | / | / | ROwater | ||
Disinfection | 3 | 93 | 150 | ROwater | ||
Drying | 15 | 60 | / | |||
11 | MetalCasing | Enzyme Washing(S) | 8 | 40 | 180 | Softwater |
1stRinsing(S) | 3 | / | / | Softwater | ||
2ndRinsing(RO) | 3 | / | / | ROwater | ||
Disinfection | 3 | 93 | 150 | ROwater | ||
Drying | 15 | 60 | / | |||
12 | Orthopedic Instrument | Enzyme Washing(S) | 8 | 40 | 180 | Softwater |
1stRinsing(S) | 2 | / | / | Softwater | ||
2ndRinsing(RO) | 2 | / | / | ROwater | ||
Disinfection | 3 | 93 | 150 | ROwater | ||
Drying | 15 | 60 | / | |||
13 | User-define Washing | Pro-Washing | 2 | / | / | Softwater |
Enzyme Washing(S) | 5 | 40 | 180 | Softwater | ||
1stRinsing(S) | 2 | / | / | Softwater | ||
2ndRinsing(RO) | 2 | / | / | ROwater | ||
Disinfection | 3 | 93 | 150 | ROwater | ||
Drying | 15 | 60 | / |
Notes:
1. Set the amount of the cleaning agent as per the instructions of the different cleaning agent
manufacture.
2. Set the washing temperature as per the instructions of the different cleaning agent.
2) Program operation
Select program as an example to explain the operating method.
• Step 1 : Power on click “Enter”
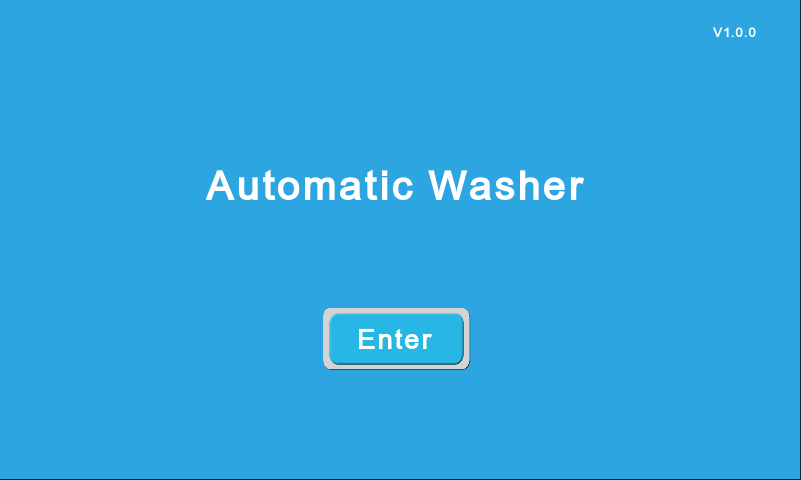
• Step 2 : After clicking on the "logo", enter the program selection page.
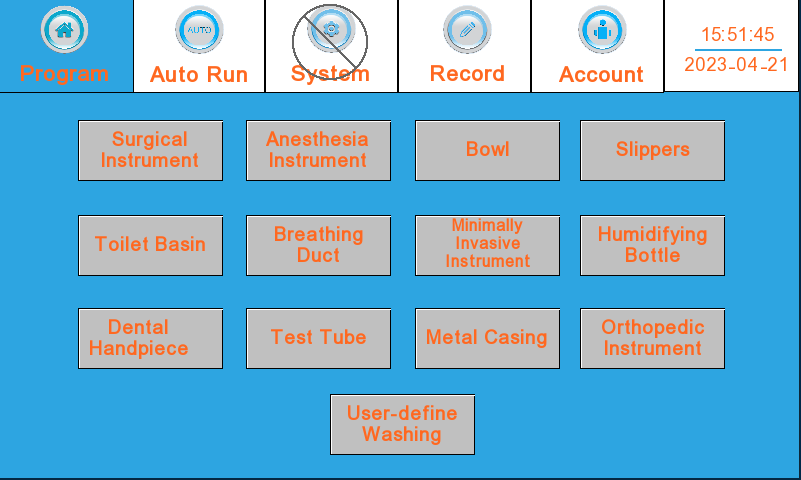
• Step 3:
1. If you do not need to make changes to the built-in program, you can directly select the program you want to use,click to select the program, and then jump to the automatic operation interface.
2. Click 'Start' and the program will start running automatically.
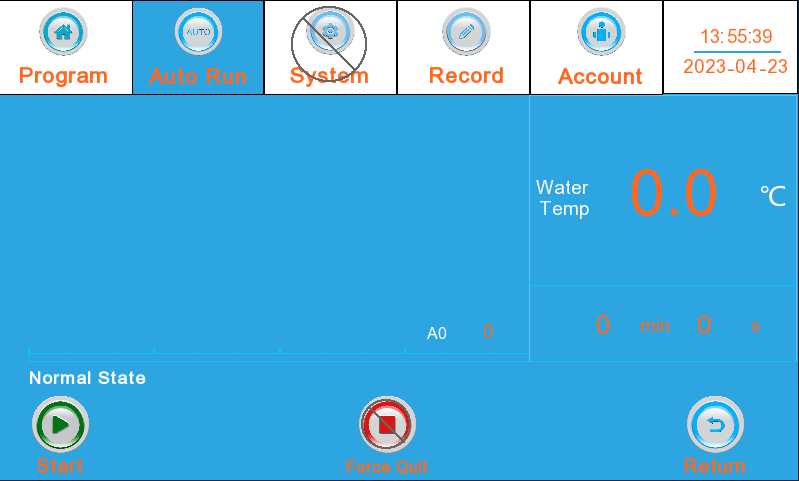
• Step 4: This machine has permission management function. If you need to make changes to the built-in program, Must obtain operator or management authority. Access: Click on "Account" and select "Password Login".
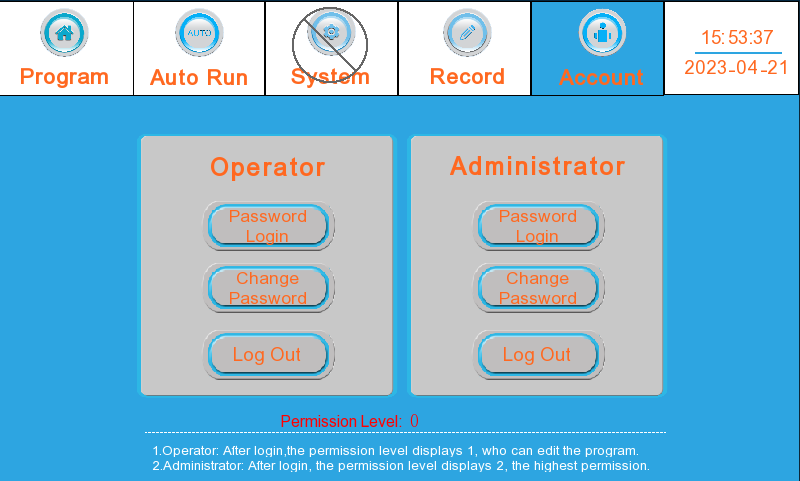
• Step 5: The initial password for 'operator' is' 111 ', The initial password for 'management personnel' is' 222 ', Click 'OK'. Click on 'Program' again.
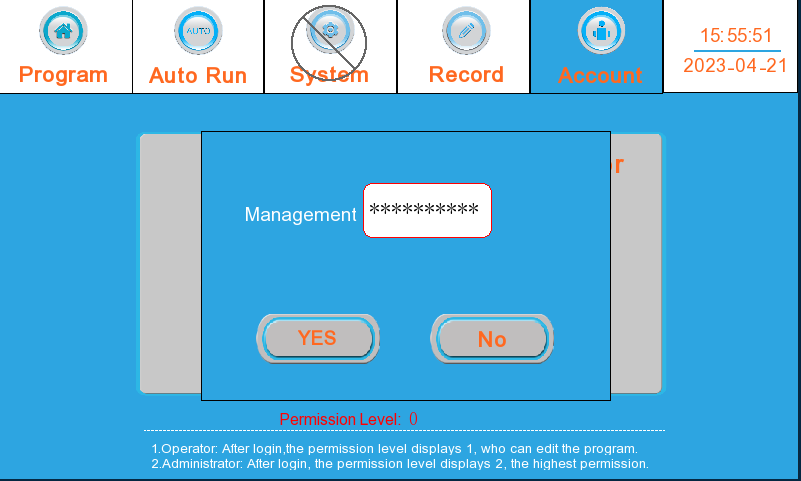
• Step 6: Enter the cleaning program interface, totaling 13 Programs available for selection, click on the program you want to use After entering the program settings page.
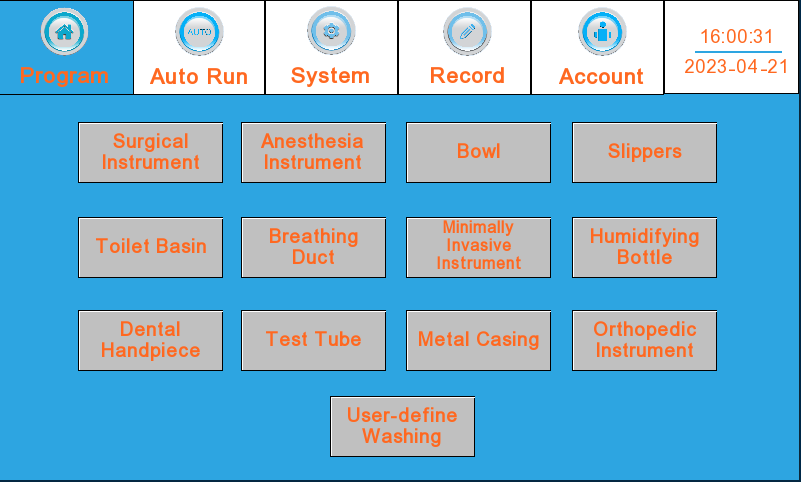
• Step7: After setting program parameters, click "Save", Click on 'Auto Run' again, click on 'Start', The program starts running automatically
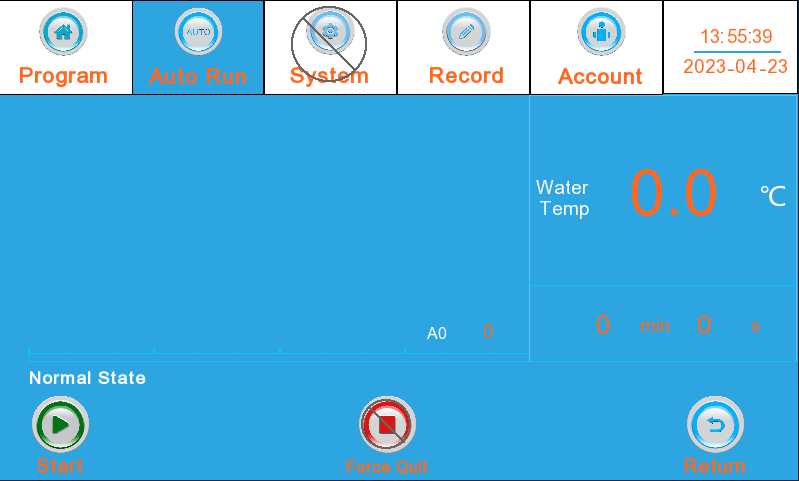
4. Manual test
• Step 1:1). After power on log in to the "Operator" or "Manager" permissions.
2). Click on 'System'.
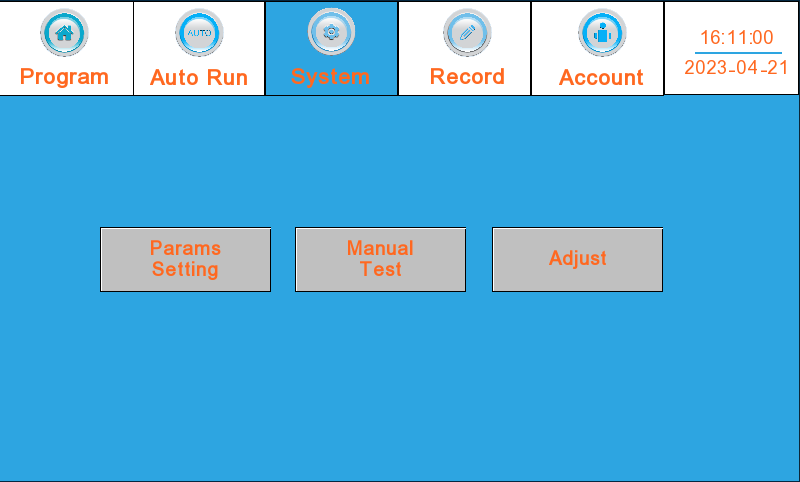
• Step 2 : Enter the manual test and click the switch button to perform a single function test.

5. Operating system
• Number of programs 13 cleaning programs: Program 1- Program 13, There are differences in the number and name of cleaning steps for each program.
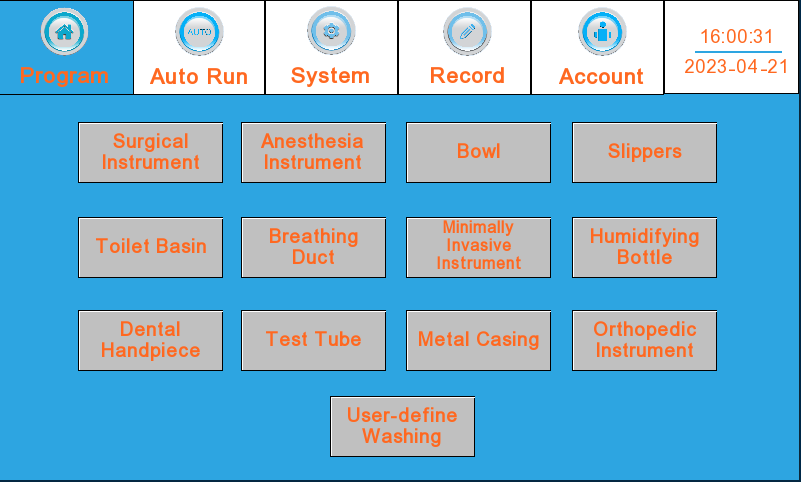
• Program parameter settings
1. A maximum of 12 steps can be set for the program, and the cleaning steps and corresponding parameters can be modified.
2. The program steps include temperature, time, and amount of additives.
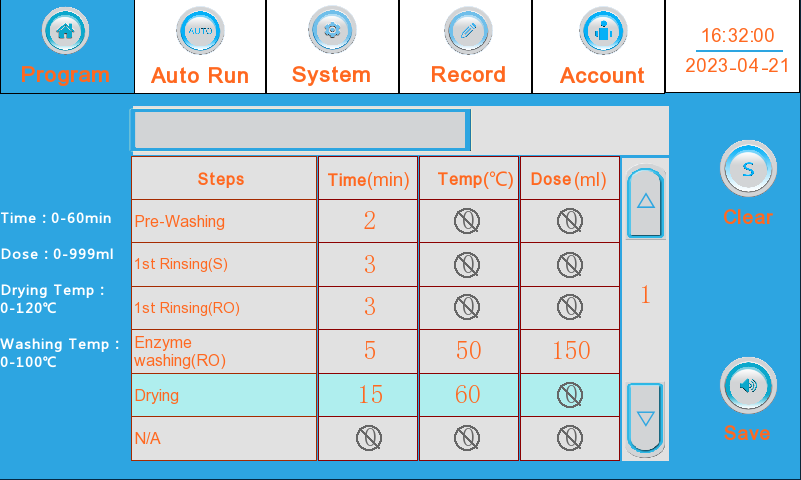
Set freely according to actual needs, and the screen setting parameters are for reference only.
• Cleaning steps:
1. Pre-Washing
2. Enzyme washing(S)
3. 1st Rinsing(S)
4. 2nd Rinsing(RO)
5. Disinfection
6. Drying
• Auto run
After the program is set, it is necessary to switch to the automatic operation interface to start the cleaning program.
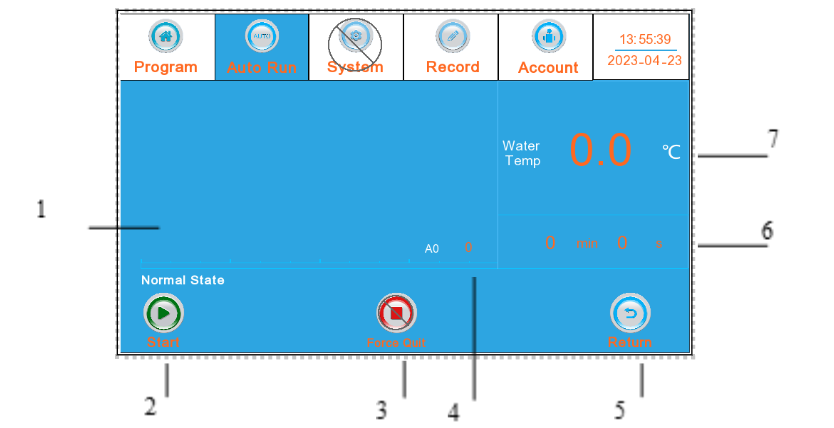
NO. | Content | Illustrate |
1 | Status information | The real-time status of the device will be displayed here if there is any alarm information. |
2 | Start | Program run start key. |
3 | Force Quit | Stop the program being executed. |
4 | Time progress bar | Real time display of the progress of program execution. |
5 | Return | Switch to the program selection screen. |
6 | Time | Accumulated running time. |
7 | Water temp | Real time cleaning temperature. |
• System
The system includes parameter settings, manual testing
Calibration (date, dose, temperature).
Note: The system functions mainly for the manufacturer's after-sales personnel)
Or user engineering personnel are conducting equipment debugging, maintenance.Use during maintenance.
We will not provide a detailed introduction here.
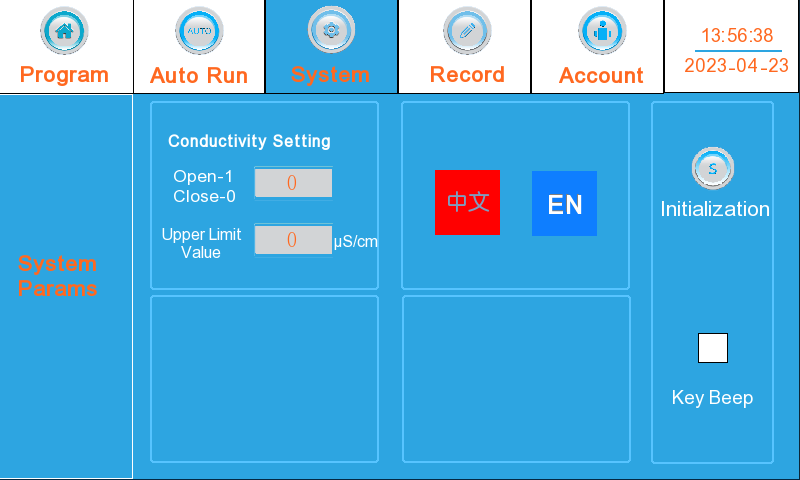
• Record
1)Cleaning Record
• Step 1 : Start up and enter the "Record" interface, click "Clean Record".
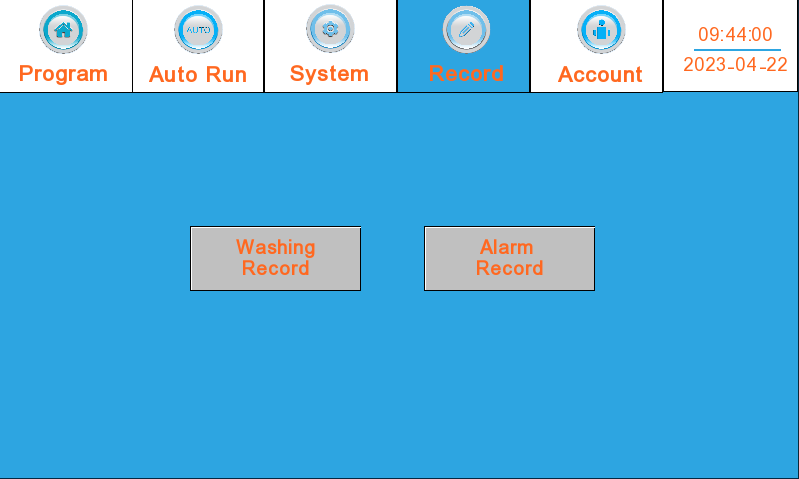
• Step2:
1) Record view: Select a cleaning record and click 'View Selected'.
2) Record export: Insert the USB drive and click 'Export Selected' or export the record.
3) Record printing: Select a cleaning record and click 'Print'.
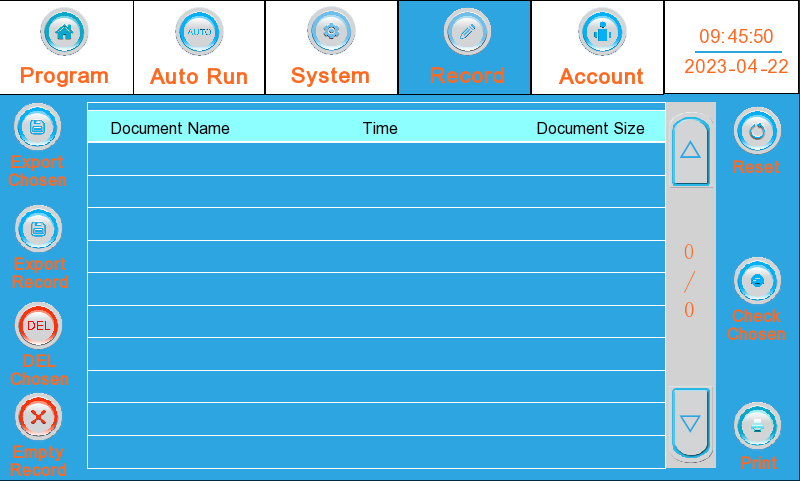
2. Alarm Record
• Step 1 : Start up and enter the "Record" interface, Click on 'Alarm Record'.
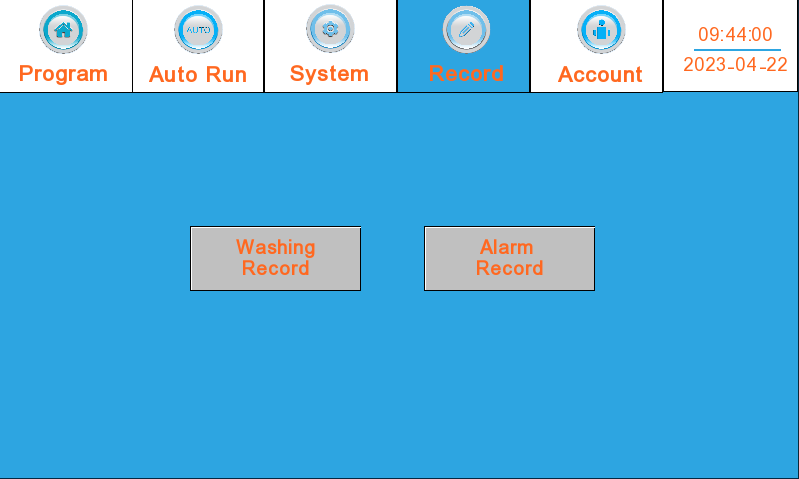
• Step 2: The alarm record is for viewing all. Alarm records are all exported.
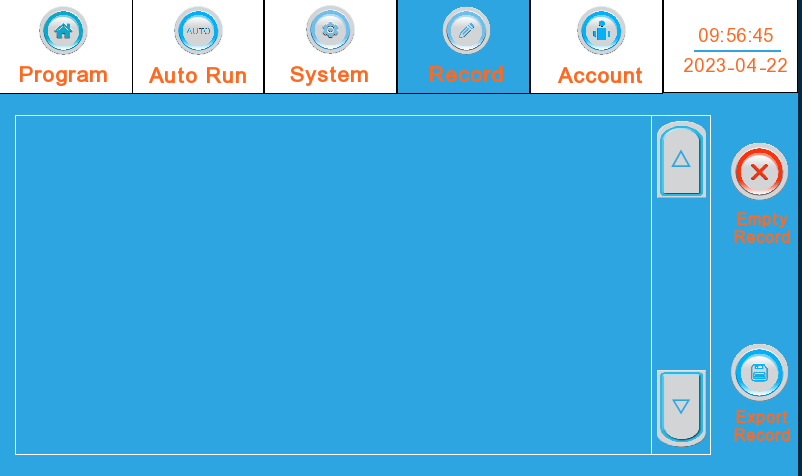
6. Password protection
1) Permission DescriptionPermission Level | Initial Password | Purview |
Level 0 permissions | None | Select to run the cleaning program and cannot modify parameters. The cleaning machine records can be viewed, exported, and printed, but cannot be deleted. Alarm records can be viewed, but cannot be deleted. |
Level 1 permissions | 111 | Capable of operating level 1 permission function Program parameters can be modified. |
Level 2 permissions | 222 | All functions can be operated. |
2) Password login
To obtain the corresponding operation permissions, you need to log in with the corresponding password, which can be set to a maximum of 8 digits.
Step 1: On the startup screen, enter the "Program"interface and click on "Account".
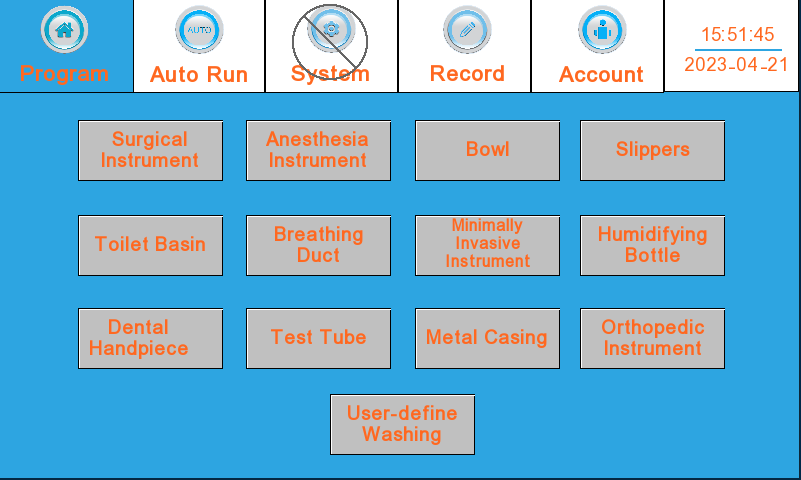
• Step 2: Click on 'Password Login'.
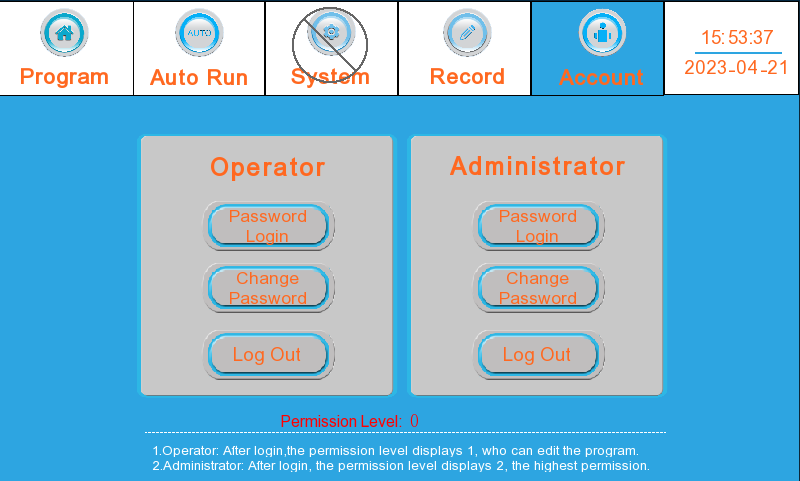
• Step 3: Enter the corresponding permission password. After entering the password, the interface will display the corresponding permission level.
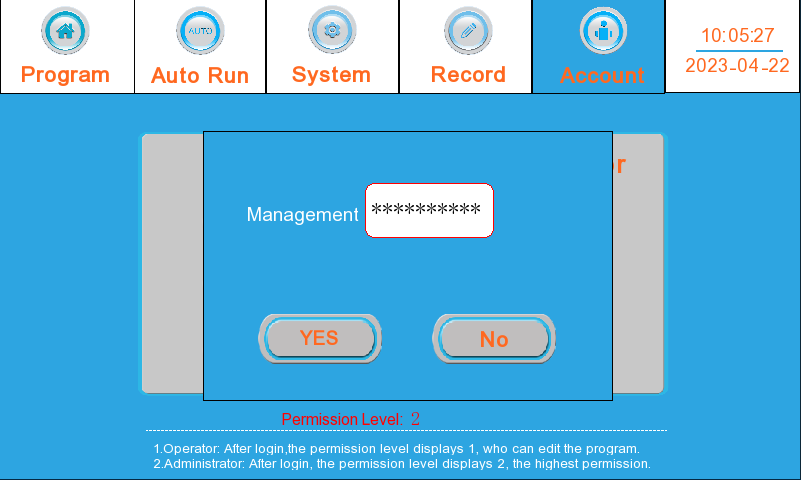
3) Password modification
• Step 1:Start up and enter the "Account" page
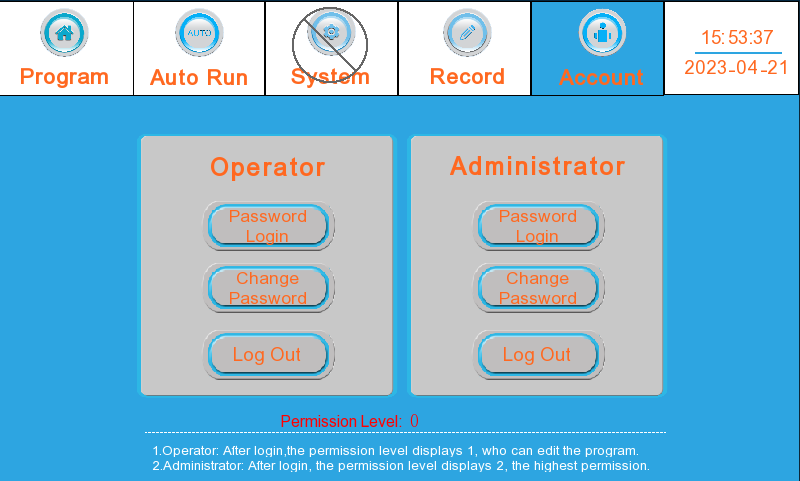
• Step 2: Select the 'Password Modification' corresponding to the account you want to modify,
Pop up a password modification window and input one by one according to the prompts. Click 'OK'.
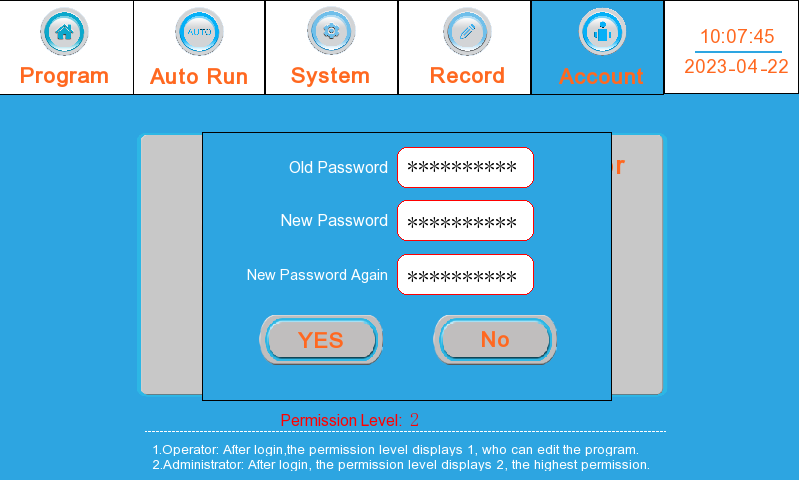
7. Single program
1) Single Programs ListProgram Name | Notes |
Pre-washing | Soft water and washing time set freely. |
Enzyme washing | Purified water with enzyme and washing time set freely. |
1st Rinsing(S) | Soft water and washing time set freely. |
2nd Rinsing(RO) | Purified water and washing time set freely. |
Disinfection | 93℃ purified water and washing time set freely. |
IV. Abnormal Conditions Treatment
1. Abnormal conditions treatment
When false happens, details will be shown on the touching display screen with buzzer alarming and yellow light of clean area twinkling. Operator can find out the cause of the false according to the detailed information and solve it.False Name | Cause | Solution |
Water heating abnormal | Water heating is time-exceeding or there’s problem with heating pipe. | Contact after-sales service staff |
Soft water inlet abnormal | Soft water inlet is time-exceeding. | |
Purified water inlet abnormal | Purified water inlet is time-exceeding. | |
Air heating abnormal | The temperature of the heater is abnormal. | |
Heat fan abnormal | Wind-discharging of the fan is abnormal or its temperature is too high. | |
Circulating pump abnormal | Drainage time is time-exceeding or it doesn’t work. | |
Water temperature abnormal | Demanded temperature cannot be reached. | |
Drying temperature abnormal | Air heater temperature is too high. | |
Front door open unlocked | Front door lock rod not pushed to position or door sensing switch damaged. | |
Back door open unlocked | Back door lock rod not pushed to position or door sensing switch damaged. | |
Lack of Enzyme Cleaning Fluid | Enzyme Cleaning Fluid has run up. | Add Enzyme Cleaning Fluid |
Lack of Lubricant | Lubricant has run up. | Add Lubricant |
Notes: If there is an alarm during operation, the program need to be restarted after the problem is solved.
2. Others abnormal situations
Abnormality | Cause | Solution |
The machine does not work. | 1. There’s no power supply. 2. Power plug is not connected well with the outlet. 3. The door of washer disinfector isn’t closed well. 4. The power switch isn’t turned on. 5. “Start” is not pressed. | 1. Turn off power switch and operate the machine after there is electricity in circuit. 2. Connect the power plug well. 3. Close the door well. 4. Turn on the power switch. 5. Press “Start”. |
Washing effect is not good. | 1.The spraying mouth is blocked by instruments. 2. Instruments are not placed properly. 3. The spraying mouth is blocked. 4. Cleaning solvent is chosen incorrectly or not used. | 1. Place instruments again. 2. Place instruments again as written in User Guide. 3. Clean the spraying mouth. 4. Use the cleaning solvent we recommended. |
There’s calcium sediment or white membrane formed. | 1. Salt in the salt container is too little. 2. Hardness of the water is too high. | Add salt. Replace water-softener with purified water device. |
3. Failure alarming reset
As per failure message shown on screen, operator can remove trouble if it could be done by himself or herself, otherwise, please call after-sales-service person.Attention: If failure occurs in period of running, when trouble is removed, program should be re-started.
V. Service And Maintenance
1. Regular Maintenance
Repair period depends on frequency the equipment is used with, and depends on physical life of equipment parts, the following show details:Part | Annual check | renewal as required | renewal annually | Renewal every 2 years |
Fan | ● | ● | ||
Water overheating protection | ● | ● | ||
overheating protection of drying cabinet | ● | ● | ||
Air check valve | ● | ● | ||
Drainage check valve | ● | ● | ||
Ejection arm spindle | ● | ● | ||
seal ring | ● | ● | ||
Socket | ● | ● | ||
Hot air inlet conduit | ● | ● | ||
Multi-enzyme cleaning agent duct | ● | ● | ||
All pipes | ● | ● |
2. Function Inspection
Inspection Information | Annual check | renewal as required |
Check if power switch runs in order, make sure the cable is in good condition | ● | ● |
Check if water heating pipe, fan, dry heating pipe, circulation pump, drainage pump, metering pump, liquid level sensor, position switch and water inlet valve runs in order. | ● | ● |
Check if seal ring is in good condition, check all pipe connection, and check if fastening and sealing is needed. | ● | ● |
Check if keys on control panel run well, and check if program runs as setting | ● | ● |
VI. Transportation
The machine can be stored no longer than 15 weeks within the following condition limits when being shipped or stored in packages:• Environmental temperature range: -40 ~ +70℃
• Air pressure range: 500~1060MPa
VII. Appendix
1. Washer disinfector placing diagram
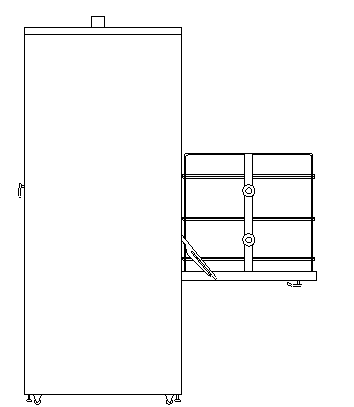
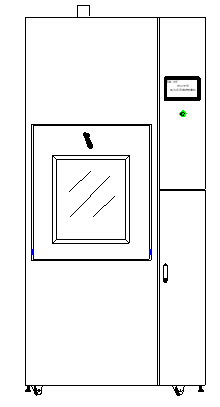
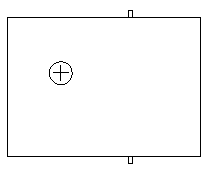
2. Ventilation & drainage installation diagram
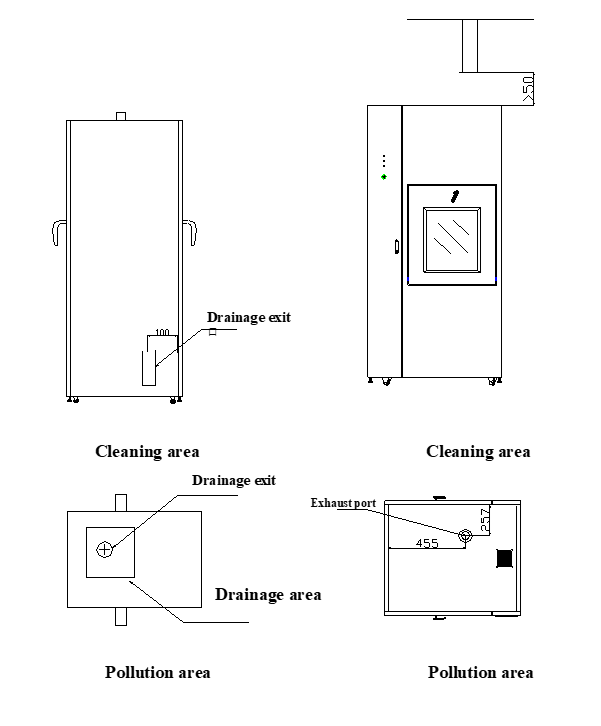
3. A0 value display
A0 value is the measurement for humidity-heat treatment fatality effect towards animalcule which refers to the destructive equivalent of humidity-heat treatment in one second under temperature of 80℃ with 10K of animalcule obtained as the reference value.Standard PrEN ISO 15883 regulates that the thermal disinfection of washer disinfector should reach medium level with A0 value no lower than 600.
A0 value comparison list:
Disinfection Time (min) | Disinfection Temperature (℃) | A0 Value |
10 | 80 | 600 |
100 | 70 | 600 |
1 | 90 | 600 |
3 | 93 | 3000 |
10 | 93 | 12000 |
… | … | … |
A0 value display
The product owns A0 value display function. When the temperature gets 80℃, the A0 value begins to be measured and will be shown on the screen. A0 value will increase as the rising of temperature and time, by which operators can judge the thermal disinfection level of the machine.
4. Liquid Agent Add
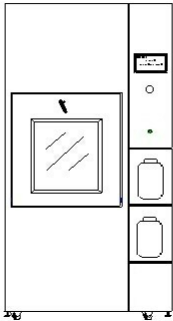
1) How to add
There will be indication message shown on the screen when the cleaning agent are insufficient. So, please add the cleaning agent accordingly when it shows indication as per following steps,
1) Open the secondary door, screw off the cap of the agent barrel, then take out the barrel as shown in Pic.16
2) Pour the liquid agent into the barrel and put the barrel back inside the washer with its cap screwed on.
3) After adding the agents, indication message on the screen would be disappeared.
2) Blending ratio
Please refer to the instructions of enzyme manufacturer and lubricant manufacturer.
VIII. Packing List
No. | Name | Unit | Quantity |
1 | Glassware Washer | Unit | 1 |
2 | Inlet water pipe | Unit | 2 |
3 | Drainage pipe | Unit | 1 |
4 | Rack | Unit | 1 |
5 | Basketry | Unit | 10 |
6 | Operation Manual | Piece | 1 |