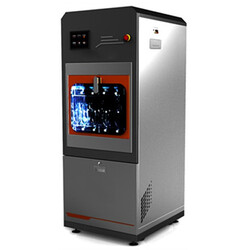
Glassware Washer BGLW-103
- Sea, Air, Door to Door Shipping
- 1 Year Warranty
- US & European Standards
Lab Automatic Glassware washer is an automatic machine for the process of washing, disinfection and drying of various laboratory equipment such as flasks, beakers, pipettes and so on. Washing carried out through air heater and HEPA filter facilitates by drying
- High efficient cleaning system, designed with European reliable pump, optimized spray arm and nozzles and self-cleaning program.
- Rapid and efficient drying system, designed with independent air heater, HEPA filter and drying process
- Water heating temperature can reach 99°C , while hot air drying temperature can reach 120°C
- Professional configuration design-stainless steel for corrosion resistance; reinforced glass window mounted to achieve a clear view on washing process
Specification
Features
Applications
Capacity | 320 L |
Water Consumption Cycle | 22 L |
Inlet Water Pressure | 0.3~0.8 Mpa |
Noise | ≤ 55 dB |
Material | Internal Material: SS316, Outer Material:SS304 |
Overall Power Consumption | 6/17 KW |
Power Consumption- Water Washing | 1.5 KW |
Power Consumption- Water Heating | 5/15 KW |
Power Consumption-Drying | 3.6 KW |
Power Supply | AC220 V, 50 Hz , 380 V ,50Hz (Standard) 110V , 60 Hz (Optional) |
Cleaning Rack | 3 pcs |
Standard Cleaning Rack | BKIR36 x 3 |
Standard Accessories | USB interface, One Bucket RBS A 156 leaner (1L), One Bucket RBS A 375 neutralizer (1L) |
Optical Accessories | Cleaning Racks |
Washer Chamber Size (WxDxH) | 600x629x820 mm |
External Size (WxDxH) | 690x790x1970 mm |
Package Size (WxDxH) | 790x940x2100 mm |
Gross Weight | 320 kg |
- High efficient cleaning system, designed with European reliable pump, optimized spray arm and nozzles and self-cleaning program.
- Rapid and efficient drying system, designed with independent air heater, HEPA filter and drying process
- Water heating temperature can reach 99°C , while hot air drying temperature can reach 120°C
- Professional configuration design-stainless steel for corrosion resistance; reinforced glass window mounted to achieve a clear view on washing process
- PLC touch screen control with present 12 programs and 99 customized programs
- Safety protection-electronic security door lock to prevent unexpected door opening , water & drying air temperature dual control and equipped with emergency switch.
Used in University , Research institution, Pharmaceutical, Chemical industry, Microbiology Lab
Operating Manual for BGLW-103

1. Code of safe operation
1.1 Electrical safety
1.2 Operational safety
1.3 Environmental safety
2. Overview
2.1 Product use
2.2 Technical parameters
3. Installation and Commissioning
3.1 Installation conditions
3.2 Installation
3.3 Power installation
4. Operation
4.1 Product schematic
4.2 Goods loading
4.3 Program setting
5. Operating system
5.1 Program
5.2 Automatic operation
5.3 System
5.4 Record
5.5 Account
6. Adding lotion
7. Maintenance
7.1 Regular maintenance
7.2 Regular inspection
7.3 Cleaning circulation system
7.4 Replacement of vulnerable parts
8. Appendix
8.1 Program setting reference
8.2. Packing list
1. Code of safe operation
1.1 Electrical safety
1) The main power switch must be equipped with current leakage protection and operated independently.2) The installation of the cleaning machine must be reliably grounded.
3) It is strictly forbidden to have the power cables extended, stretched, knotted or squeezed.
4) Please be sure to disconnect the main power supply of the cleaning machine when repairing and maintaining, and do not operate it with power.
5) When the Cleaning Machine is unattended or not used for a long time, make sure to cut off the main power supply.
1.2 Operational safety
1) Do not open the door of the cleaning chamber forcibly during the operation of the cleaning machine to avoid personal injury caused by the overflow of hot water and hot air.2) When an emergency occurs, press to cut off the main power supply or "emergency stop switch", and then perform other operations after the water and air temperatures drop to a safe temperature.
3) If there is a sudden shutdown, abnormal noise, or peculiar smell during the use of the cleaning machine, shut down the cleaning machine immediately for inspection or contact the manufacturer's after-sales service for maintenance.
1.3 Environmental safety
1) Do not install and use the cleaning machine in an environment with flammable and explosive gas or liquid.2) This product is a cleaning equipment and cannot reprocess the waste water after cleaning. The user shall dispose of the waste water by himself to meet environmental protection emission requirements.
2. Overview
2.1 Product use
The automatic utensil cleaning machine is also known as the laboratory bottle washing machine (hereinafter referred to as the cleaning machine), which is applicable to washing conventional glassware in the laboratories of pharmaceutical, food and chemical enterprises, universities, scientific research institutions, and testing institutions, such as test tube, beaker, flask, graduated cylinder, pipette, petri dish, sample injection bottle, and conical flask.2.2 Technical parameters
Model Goods | BGLW-101 | BGLW-102 | BGLW-103 | ||
Overall dimension W×D×H mm | 980×740×870 | 690×790×1820 | 690×790×1970 | ||
Maximum cabin size W×D×H mm | 600×629×465 | 600×629×690 | 600×629×820 | ||
Effective cabin size W×D×H mm | 570×600×420 | 570×600×600 | 570×600×760 | ||
Voltage (V/Hz) | 220/50 | 220/50 | 380/50 | 220/50 | 380/50 |
Water heating power (kW) | 5 | 5 | 15 | 5 | 15 |
Circulating pump power (kW) | 0.75 | 0.75 | 1.5 | ||
Drying fan (kW) | 0.25 | 0.75 | 0.75 | ||
Drying power (kW) | 3 | 3.6 | 3.6 | ||
Total operating power (kW) | 6 | 6 | 17 | 6 | 17 |
Water inlet pressure (MPa) | Tap water: 0.3~0.8 RO water: 0~0.8 |
3. Installation and Commissioning
3.1 Installation conditions
Goods | Installation conditions |
Environment | Temperature: 5°C~35°C; Humidity: ≤85%; Atmospheric pressure: 80 kPa~106 kPa; Note: Avoid using in flying dust, dust, vibration and outdoor environment; |
Power supply | A separate circuit breaker or control switch must be connected, and the grounding cables must be firm. 1.5 meters above the ground. |
Water source | Water inlet pressure: tap water 0.3~0.8MPa, RO water 0~0.8MPa. RO water, tap water. 1.5 meters above the ground. |
Water drainage | The diameter of the sewage outlet shall not be less than 55mm and shall not be 5cm above the ground. |
Location | The installation location shall be no more than 2 meters away from the power source and water source. |
Ground | The ground shall be flat, and the height difference within 1m 2 shall be less than 5mm. Ground load ≥ 1 ton/m 2 . |
3.2 Installation
1) Equipment in place- Remove the outer packing box and put the cleaning machine to the installation position.
- Adjust the height of the feet to make the four supporting feet touch the ground and adjust the cleaning machine to be level.
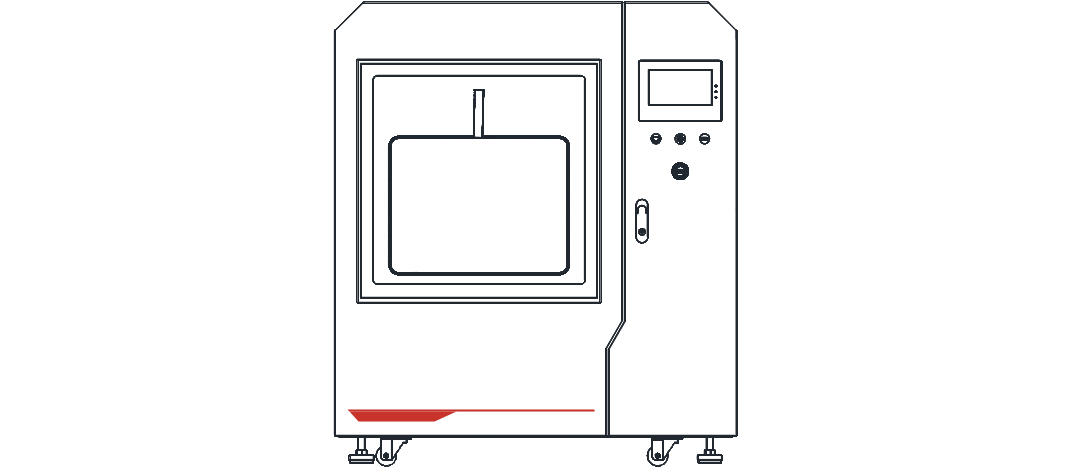
BGLW-101
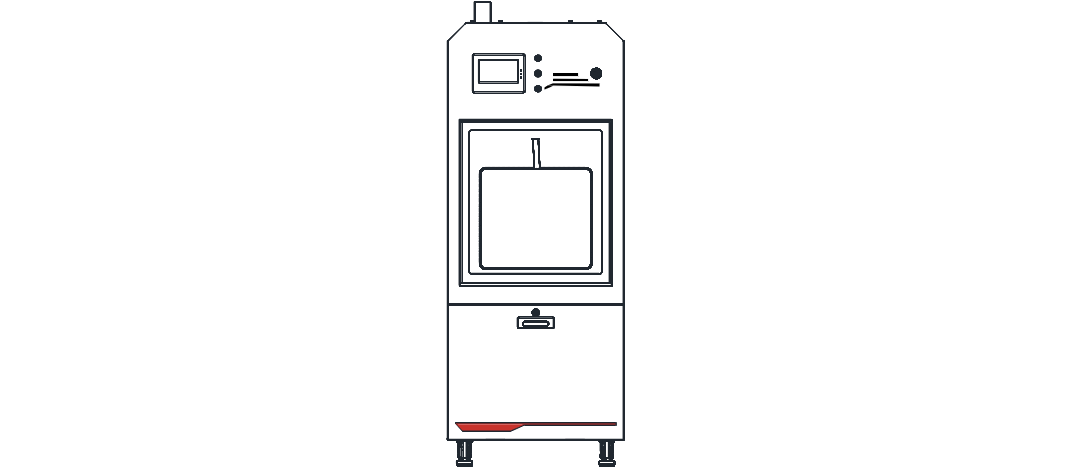
BGLW-102 & BGLW-103
3.3 Power installation
![]() | Electrical installation must be completed by a professional electrical engineer. |
The power switch must be used independently and has a leakage protection function. | |
The power supply must have a reliable grounding wire. | |
Check the connection tightness after the power cord is connected. |
Please configure the corresponding leakage protection switch according to the following requirements for different models of cleaning machines.
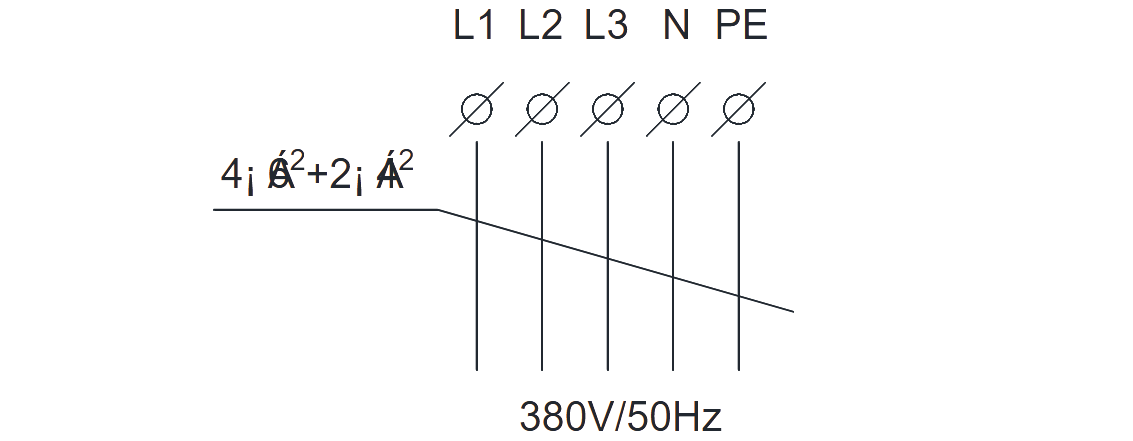
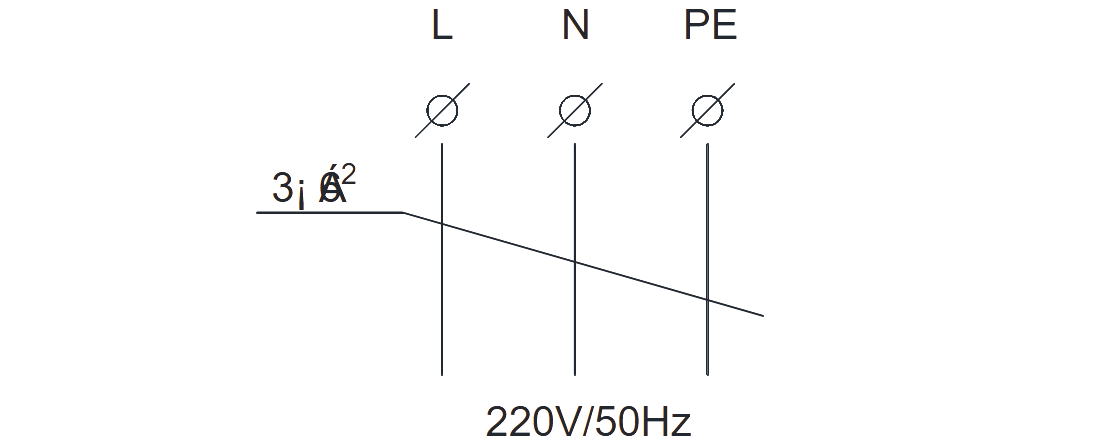
Notice:
1) Do not directly stack the power cord on the ground.
2) The water inlet pipe and power cord of the cleaning machine shall be located on the back of the cleaning machine. Please do not put the power cord on the water source pipe.
2.3 Inlet and drainage installation
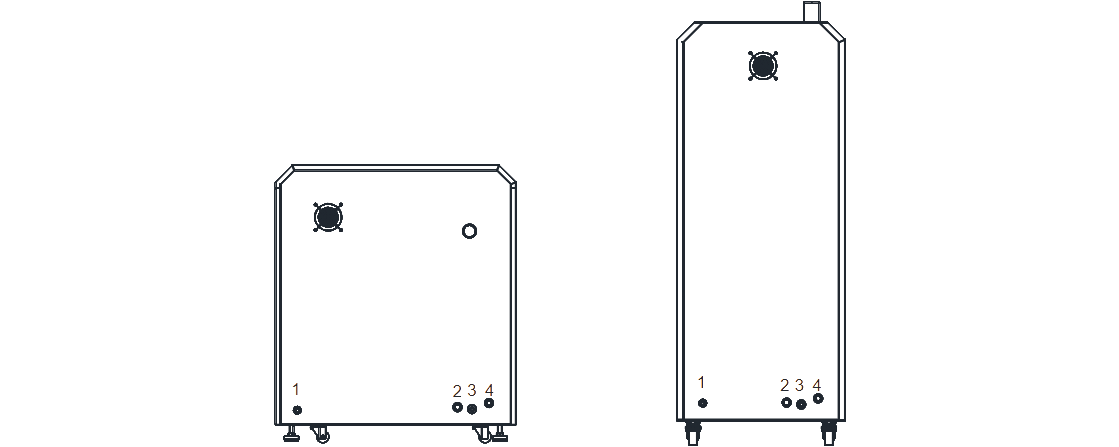
BGLW-101 BGLW-102 & BGLW-103
1. Main power cord
2. Drain outlet
3. RO water valve
4. Tap water valve
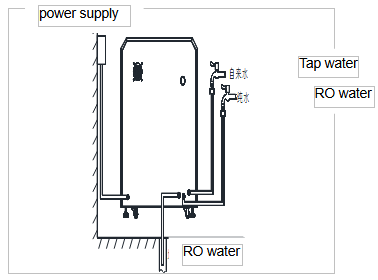
• Installation of RO water inlet pipe
Connect one end of the 6-point thread to the RO water inlet valve, and connect the other end of the quick coupler to the tap;
• Installation of tap water inlet pipe
Connect one end of the 6-point thread to the RO water inlet valve, and connect the other end of the quick coupler to the tap;
• Installation of drainage pipe
Insert one end of the drain pipe into the drain outlet of the cleaning machine,and install and lock it with the accompanied clamp. Connect the other end to the drainage floor drain, and the connection length shall exceed 10cm to prevent the drain pipe from coming out of the drain outlet.
(Note: The drainage floor drain must be lower than the equipment drain outlet).
Note: After the inlet and drain pipes are connected, please turn on the water source and drain pump respectively to check if there is any leakage in the water pipe connection!
4. Operation
4.1 Product schematic
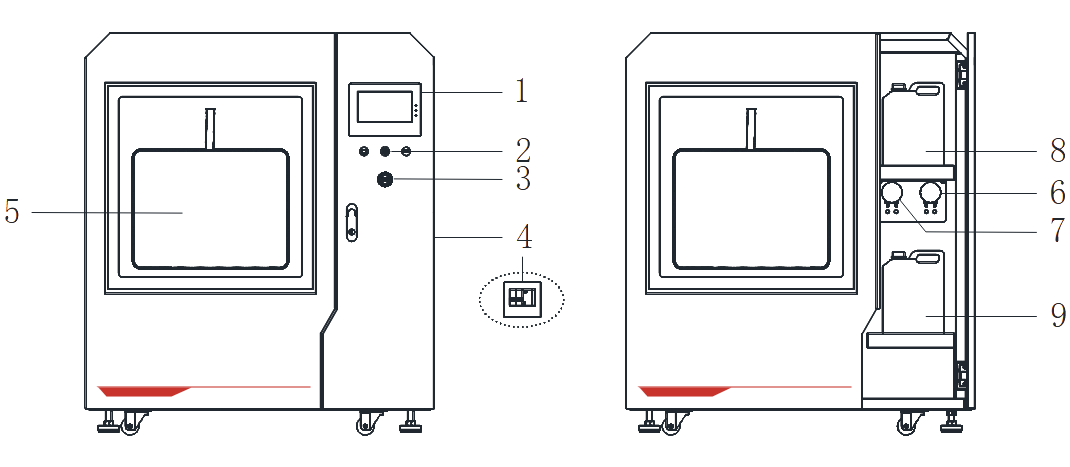
BGLW-101
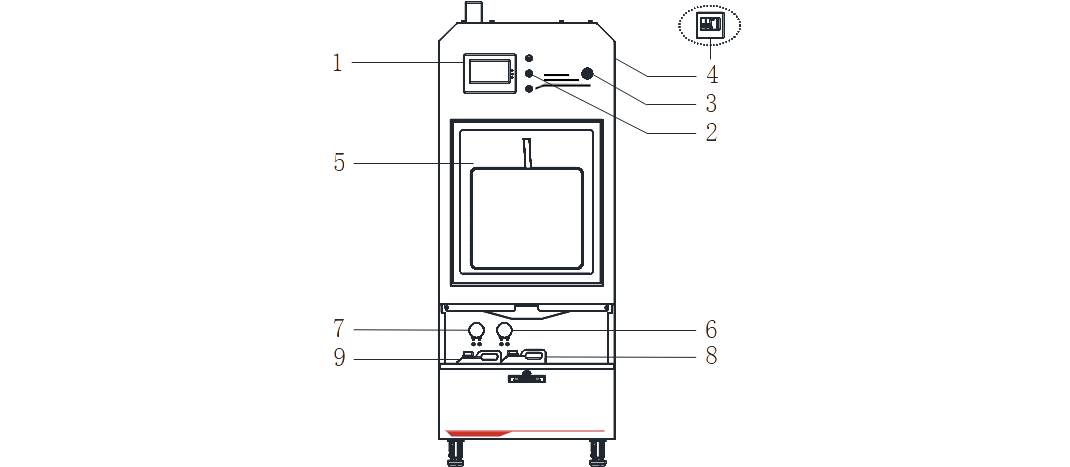
BGLW-102 & BGLW-103
1. LCD touch screen 2. On/off button 3. Emergency stop switch 4. Main power switch
5. Sealed door 6. Filling pump of cleaning liquid7. Filling pump of neutralizing liquid
8. Cleaning liquid storage barrel ; 9. Neutralizing liquid storage barrel
4.2 Goods loading
1) Installation of upper cleaning rack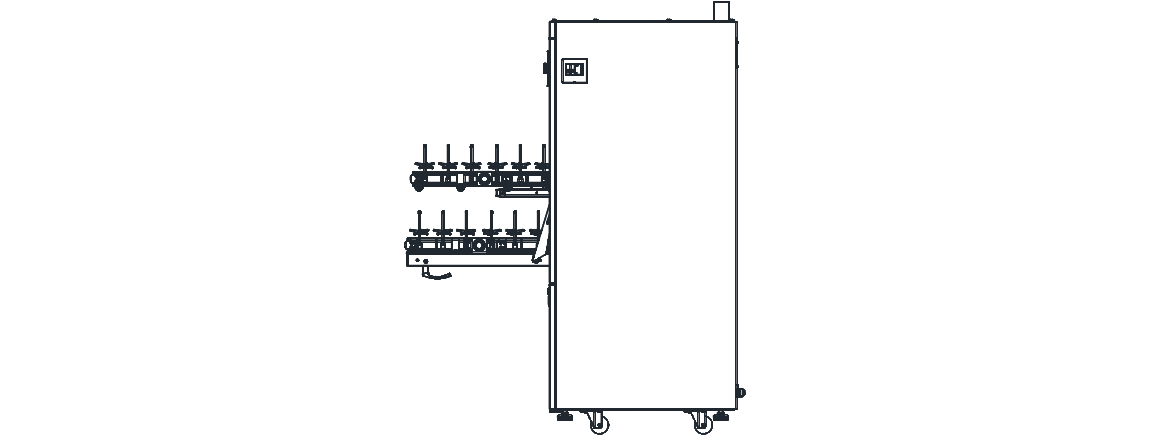
• Step 1
Slide the slide rails on both sides to the maximum position.
• Step2
Place the cleaning rack on the slide rail, make sure that the two positioning columns "1" on both sides of the cleaning rack fall into the positioning grooves "2" of the slide rails on both sides (see the figure below)
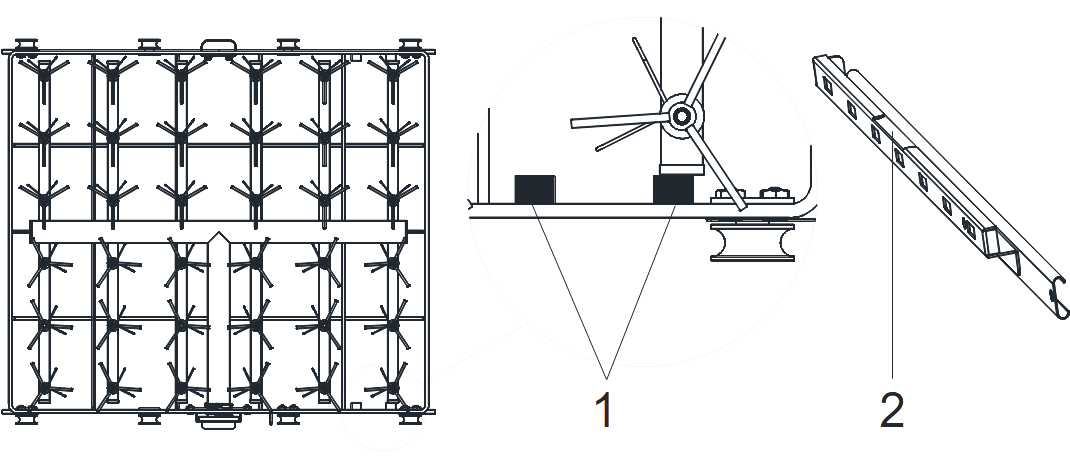
2) Utensil loading
See the table below for the maximum height of utensils loaded in each cleaning rack.
Model | BGLW-101 | BGLW-102 | BGLW-103 | |
Number of cleaning racks (layers) | 1 | 2 | 3 | |
Effective height of upper layer (mm) | / | 240 | 225 | |
Effective height of middle layer (mm) | / | 225 | ||
Effective height of lower layer (mm) | 345 | 225 | 115 |
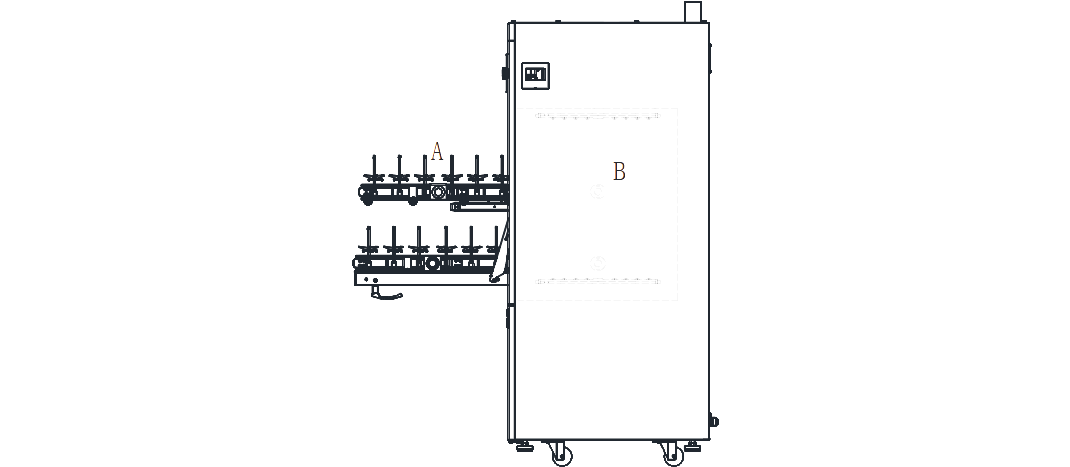
1) Open the door to a horizontal position.
2) Place the upper and lower cleaning racks on the sliding rail of the cleaning rack and the door of the cleaning machine respectively.
3) Put the Goodss to be cleaned upside down on the cleaning rack and then send the cleaning rack into the cleaning room.
4) After the door is closed, turn the handle 90° clockwise to lock the door.
Notice:
1) Under normal circumstances, the water inlet A of the cleaning rack and the water outlet B of the cleaning room are closely connected.
3) The Goodss to be cleaned shall not touch the spray arm at the top to prevent it from obstructing the rotation of the spray arm.
4) The diameter of the utensil loaded shall not be greater than the distance between the two spray columns.
4.3 Program setting
1. Standard programChoose the "Standard Washing" program as an example.
Step name | Time (min) | Temperature (℃) | Volume of lotion (ml) |
Pre-cleaning | 2 | Room temperature | * |
Cleaning with cleaning liquid (RO) | 10 | 60 | 80 |
Cleaning with neutralizing liquid (RO) | 5 | 50 | 50 |
Rinsing (RO) | 2 | * | * |
Drying | 10 | 60 | * |
• Step 1: Power on, click "LOGO" (Note: The default Chinese version) | ![]() |
• Step 2: Click "Account" and select "Password Login" (Note: Since this machine has the authority management function, the first operation requires a password to log in to obtain the authority.) | ![]() |
• Step 3: The initial password of the "Operator" is "111", The initial password of the "Administrator" is "222", Click "OK". Then click "Program". | ![]() |
• Step 4: Click "Standard Washing". | ![]() |
• Step 5: Set the cleaning parameters according to the above table. After setting, click "Save", and then click "Auto Run". | ![]() |
• Step 6: Click "Start" to start running. | ![]() |
2. Custom program
Compared with the standard program, the custom program can set the program name, and the other operations are the same as the 3.1 method. Set the program name as follows:
• Step 1: After logging in, go to the "Program" interface and click "Custom". | ![]() |
• Step 2: Click the name box to pop up the input window, and the default is English input. (Click the "CH" key to switch to Chinese input.) | ![]() |
• Step 3: Enter "Test tube", and select the corresponding number on the keyboard according to the serial number before the text to select the text. (Note: Up to 12 characters can be entered for the name.) | ![]() |
• Power-off memory function
This product has a power-off memory function. If the equipment is powered off for some reason during operation and is powered on again within 15 minutes, the equipment will automatically prompt whether to re-execute the cleaning program before the power failure.
5. Operating system
5.1 Program
• Number of programs Cleaning program: Quick washing, standard washing, enhanced washing, heavy oil washing, organic washing, plastic washing, blood washing, oil washing, inorganic washing, glass washing, rinsing, custom (1-99 programs can be set). | ![]() |
• Program steps 1) The cleaning steps and corresponding parameters of the 12 programs can be modified. 2) Program steps can be set up to 12 steps. The page can be switched through the page up and down keys. | ![]() |
• Custom program The custom program can be set, the program name can be modified, and up to 99 groups of programs can be stored | ![]() |
• Selection of custom program Click "←" or "→" on the right side of the program name to switch the custom program, click the middle number, and enter the program number (1-99) to directly enter the program. | ![]() |
• Cleaning steps 10 cleaning steps: • Empty (no settings) • Pre-cleaning • Rinsing (tap) • Rinsing (RO) • Rinsing with hot water (up to 93°C) • Cleaning with cleaning liquid (RO) • Cleaning with neutralizing liquid (RO) • Cleaning with cleaning liquid (tap) • Cleaning with neutralizing liquid (tap) • Drying | ![]() |
(Note: "tap" means to use tap water. "RO" means to use RO water. Tap water is used by default for pre-cleaning. RO water is used by default for hot water disinfection.) |
5.2 Automatic operation
After the program setting is completed, it is necessary to switch to the automatic operation interface to start the cleaning program.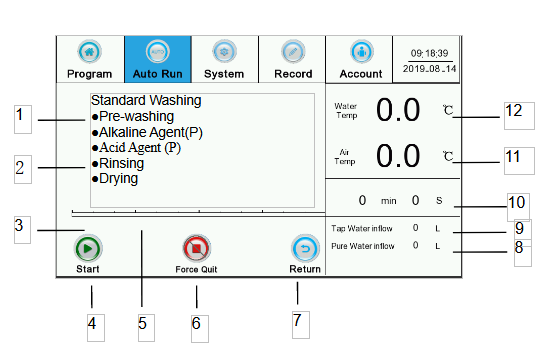
Number | Goods | Description |
1 | Program name | Display the name of the selected program. |
2 | Program steps | Display all steps of the currently running program. |
3 | Equipment status | The real-time status of the equipment. If there is an alarm message, it will be displayed here. |
4 | Start-up | Program running start key. |
5 | Time progress bar | Display the time progress of the program in real time. |
6 | Force to exit | Stop the program being executed. |
7 | Return | Return to the program selection interface |
8 | RO water inflow | Display the water inflow in the current step in real time. |
9 | Tap water inflow | Display the water inflow in the current step in real time. |
10 | Time | Cumulative running time. |
11 | Air temperature | Real-time drying temperature. |
12 | Water temperature | Real-time cleaning temperature. |
5.3 System
The system includes parameter setting, function test, and calibration (date, dose, and temperature). | ![]() |
(Note: The system function is mainly used by the manufacturer's after-sales personnel or user engineering personnel when commissioning, repairing, and maintaining the equipment. It will not be described in detail here.) |
5.4 Record
1) Cleaning records• Step 1: Power on to enter the "Record" interface, click "Cleaning Record". | ![]() |
• Step 2: 1) Record view: select a cleaning record and click "View and Select". 2) Record export: Insert a U disk, click "Export Selected" or export the record. 3) Record printing: select a cleaning record and click "Print". | ![]() |
(Note: The record export button will only be displayed when a U disk is inserted.) |
2) Alarm record
• Step 1: Power on and enter the "Record" interface, and click "Alarm Record". | ![]() |
• Step 2: All alarm records are viewed. All alarm records are exported. | ![]() |
5.5 Account
1) Permission descriptionAuthority level | Initial password | Scope of authority |
Level 0 permission | None | If the cleaning program is choosed to run, the parameters cannot be modified. The cleaning machine records can be viewed, exported, and printed, but such records cannot be deleted. The alarm records can be viewed, but such records cannot be deleted. |
Level 1 permission | 111 | Operational Level 1 permission function Program parameters can be modified. |
Level 2 permission | 222 | All functions can be operated. |
2) Password login
The corresponding password need to be logged in in order to obtain the corresponding operation authority. The password can be set up to 8 digits.
• Step 1: Power on to enter the "Program" interface, and click "Account" | ![]() |
• Step 2: Click "Password Login". | ![]() |
• Step 3: Enter the corresponding authority password. After the password is entered, the interface will display the corresponding authority level. (Note: Without obtaining the corresponding authority, the functions with cannot be operated.) | ![]() |
3) Password modification
• Step 1: Power on to enter the "Account" interface | ![]() |
• Step 2: Select the "Password Modification" corresponding to the account to be modified, and a password modification window will pop up. Enter new password one by one as prompted. Click "OK". | ![]() |
6. Adding lotion
When the amount of lotion is insufficient, there will be an alarm on the screen to prompt adding lotion. Please add lotion by the steps below: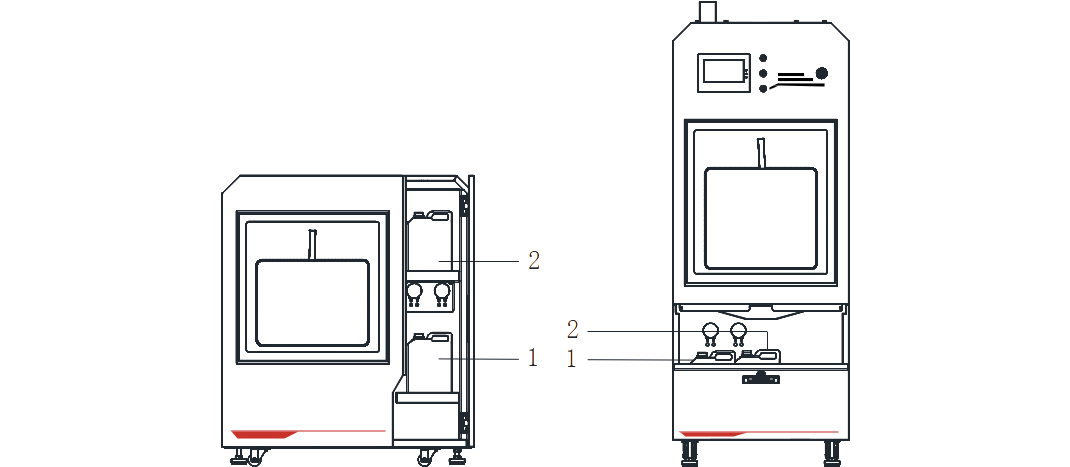
BGLW-101 BGLW-102 & BGLW-103
• Step1:
Open the door, unscrew the lid of the liquid storage barrel, take out the barrel, and add the corresponding type of lotion (In the figure, 1 is the neutralization liquid storage barrel, and 2 is the cleaning liquid storage barrel).
• Step2:
Pour the lotion into the barrel, screw on the lid and put the barrel back in place.
7. Maintenance
7.1 Regular maintenance
Number | Part | 1 month | 3 months | 6 months | Maintenance as needed |
1 | Clean the chamber filter | ● | |||
2 | HEPA filter | ● | |||
3 | Inlet valve filter | ● | |||
4 | Lotion catheter | ● | ● | ||
5 | Clean and wipe the shell of the cleaning machine | ● |
7.2 Regular inspection
The inspection cycle depends on the frequency of equipment use and the physical life of the equipment components themselves. The following is the periodic table of component inspection.Number | Part | 3 months | 6 months | Year |
1 | Main power switch | ● | ||
2 | Main power cable | ● | ||
3 | Door seal | ● | ||
4 | Emergency Stop Switcl | ● | ||
5 | Peristaltic pump of cleaning liquid | ● | ||
6 | Peristaltic pump of neutralizing liquid | ● | ||
7 | Water heating protection switch | ● | ||
8 | Air heating protection switch | ● | ||
9 | Door sensor switch | ● | ||
10 | Radiator fan | ● | ||
11 | Plastic parts of spray arm | ● |
7.3 Cleaning circulation system
1) Self-cleaning programThe self-cleaning cleaning program is mainly used for cleaning water circulation pipelines and cleaning chambers.
• Step 1: After logging in, go to the "Program" interface and click "Self-cleaning". | ![]() |
• Step 2: Set the cleaning time and temperature, and click "Start". • Step 3: After the automatic water addition is completed, click "Open Door", open the door of the cleaning machine, pour a certain amount of descaling agent into the cleaning chamber, and close the door. • Step 4: Click "Descaling Agent Addition is Completed" to start automatic cleaning. | ![]() |
2) Cleaning cleaning rack
Take CWIR222 cleaning rack as an example
Goods | Method |
Cleaning water distribution pipe | Use a Phillips screwdriver to unscrew the screws at the bottom of the 2 position, remove the silicone plug of the cleaning rack, and clean the water distribution pipe with a brush. Then press and install the silicone plug. |
Cleaning spray pipe | Unscrew the spray pipe with a wrench, and use a steel wire rod to clean from the top of the spray column from top to bottom |
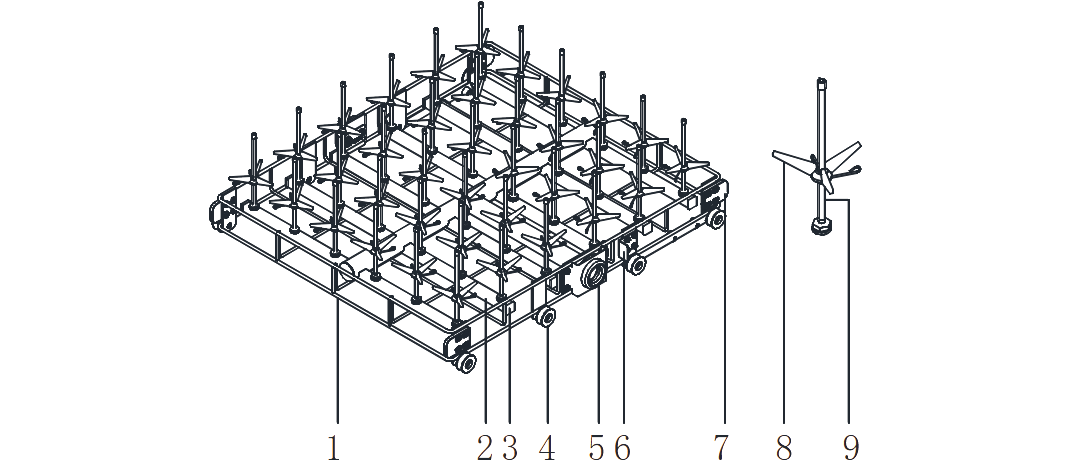
1. Steel wire frame 2. Water diversion square pipe 3. Silicone plug
4. Washing rack wheel 5. Water inlet plastic parts 6. Side stopper
7. Limit block 8. Bracket 9. Spray pipe
3) Cleaning filter
A filter is installed at the bottom of the cleaning chamber. Please clean the residue on the filter regularly to avoid clogging the filter and affecting the cleaning effect. The following figure is a schematic diagram of the location of the filter.
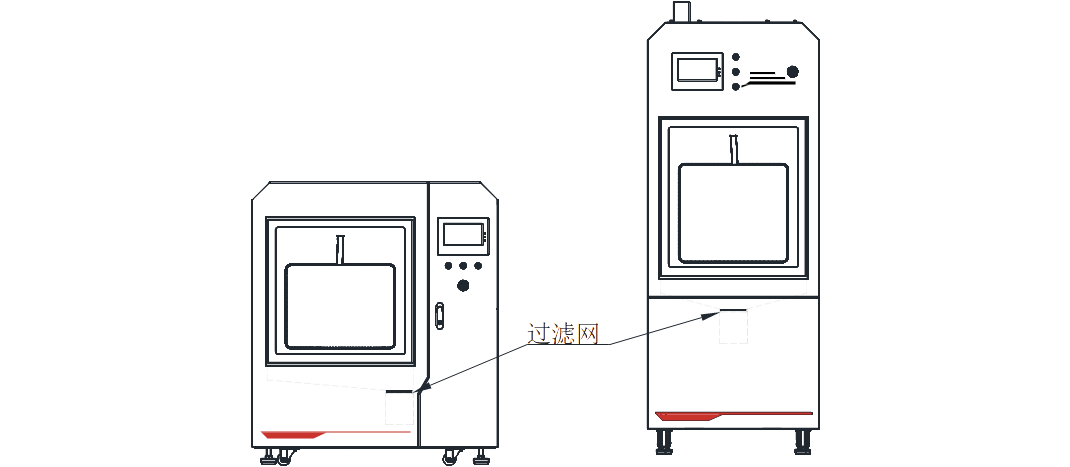
BGLW-101 BGLW-102 & BGLW-103
7.4 Replacement of vulnerable parts
1. .Replacement of lotion catheter1) Replace the suction tube between the lotion barrel and the metering pump. Disassemble the plastic clips at both ends of 8 and replace the silicone tube with the same length.
2) Replace the injection tube between the metering pump and the wall of the cleaning chamber. Disassemble the plastic clips at both ends of 5 and replace the silicone tube with the same length.
3) After the new tube is replaced, lock and fix the plastic clips.
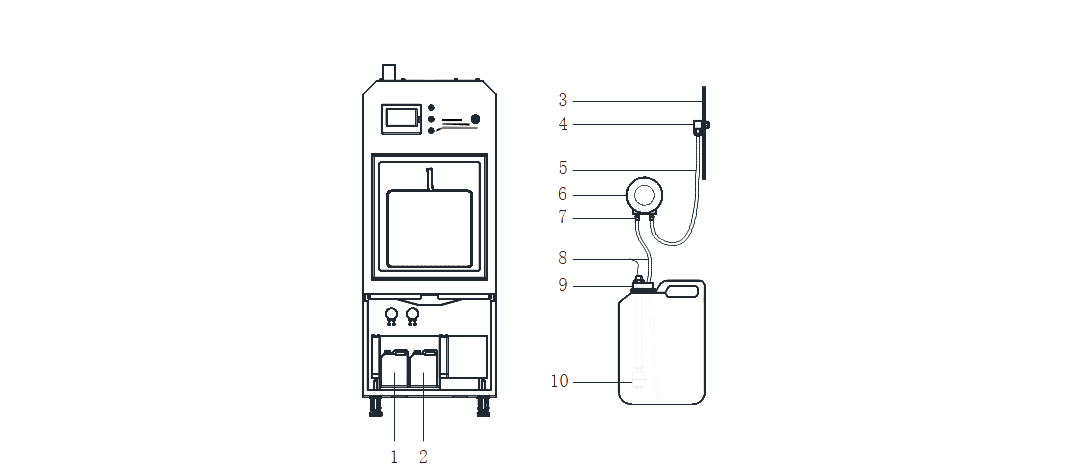
Number | Name | Number | Name |
1 | Neutralizer barrel | 2 | Cleaning agent barrel |
3 | Side wall of cleaning chamber | 4 | Stainless steel fixed seat |
5 | Drainage liquid silicone hose of peristaltic pump | 6 | Peristaltic pump |
7 | Plastic clip | 8 | Suction liquid silicone hose of peristaltic pump |
9 | Lotion sealing cap | 10 | Level switch |
2. Replacement of high-efficiency filter
• Step 1:
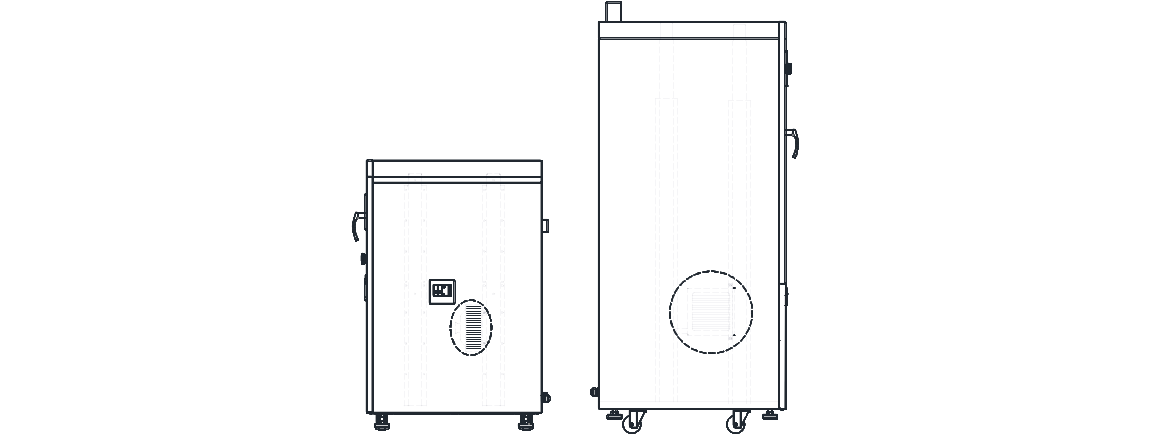
Open the housing of the cleaning machine to find the installation location of the filter.
1) CTLW-120/200 needs to open the right side panel, and fix the high efficiency filter on the rear column.
2) CTLW-220/320 needs to open the left side panel, and fix the high efficiency filter on the front column.
• Step 2:
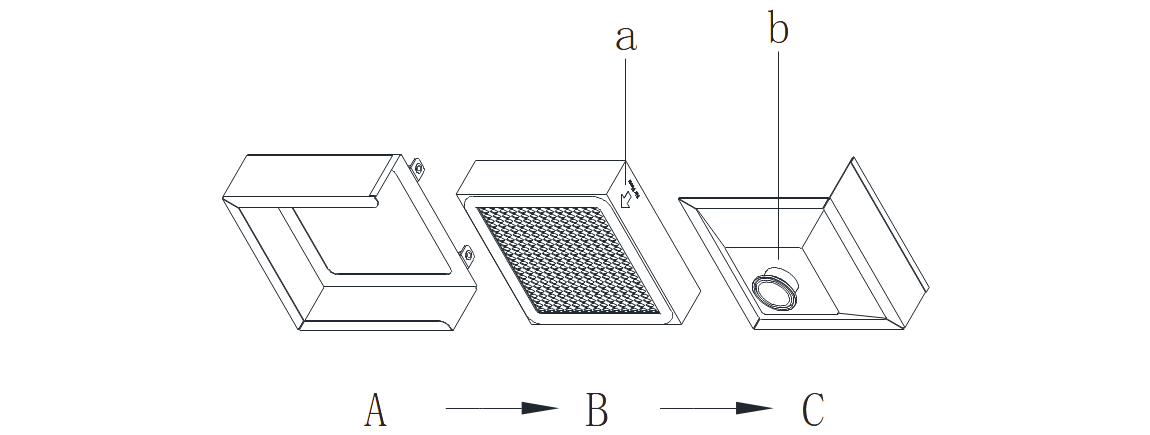
1) Separate the installation box of the high-efficiency filter from the air inlet pipe.
2) Remove the high-efficiency filter module (including A, B, and C) from the column.
3) Open the filter installation box in the direction of → and take out the filter.
4) Assemble the filter in reverse order after replacing it.
(Note: The arrow a in the figure shows the installation direction of the filter, which shall be consistent with the direction b (the connection port of the filter installation box and the fan).)
5. Alarm and prompt
This equipment is equipped with a variety of fault alarms and information prompts, which will be displayed on the touch screen in the form of text.
Information tip
Figure
E2: Water heating protection switch
1) Description:
a) The temperature of the temperature measuring element Pt100 of the air heating box is too high.
b) The temperature of the temperature measuring element Pt100 of the air heating box is damaged or the connection line is loose.
2) Treatment method:
a) Open the sealed door to check whether there is water in the cabin. If there is no water, observe whether the heating pipe is working. If it keeps working, please turn off the main power switch and contact after-sales personnel.
b) Open the sealed door to check whether there is water in the cabin. If there is water, check whether the wiring of the temperature measuring element is loose. If the wiring is not loose, replace the Pt100 air heating box.
E3: Lack of cleaning agent
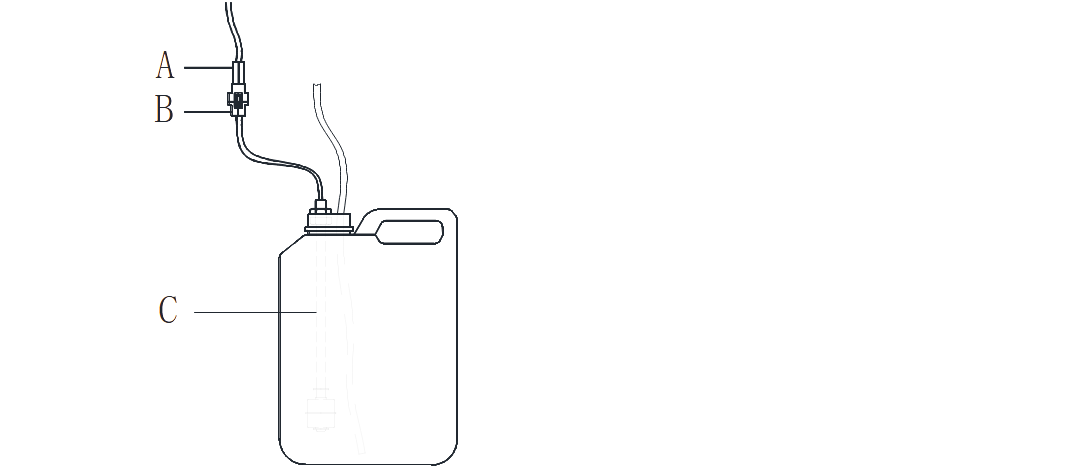
1) Description: Need to add cleaning liquid or the level switch is damaged.
2) Treatment method:
a) Add cleaning liquid.
b) Replacing the level switch: Open the A and B wire block connectors, and take out and replace B, C as a whole.
E4: Lack of neutralizing agent
1) Information description: The neutralizing liquid is used up or the level switch is damaged.
2) Treatment method: same as E3.
E5: Air heater overheating protection
1) Description:
a) The temperature of the temperature measuring element Pt100 of the air heating box is too high.
b) The temperature of the temperature measuring element Pt100 of the air heating box is damaged or the connection line is loose.
2) Treatment method:
a) Enter the "System"-"Functional Test" page, click "Fan" until the temperature of the drying box drops below 70°C, click "Fan" again to stop, and the equipment can be used at this time;
b) If the operating temperature does not drop significantly according to Step a), check whether the wiring is loose. If the wiring is not loose, replace the Pt100 air heating box.
c) Please power off and contact after-sales personnel.
E6: Circulating pump overheating
1) Description: The working current of the circulating pump is greater than the normal requirement or the circulating pump is damaged.
2) Treatment method:
a) Check whether the main power supply voltage is within the normal range. If it is out of range, please adjust the main power supply first.
b) Please contact after-sales service.
E7: Fan overheating
1) Description: The working current of the fan is greater than the normal requirement or the fan is damaged.
2) Treatment method:
a) Check whether the main power supply voltage is within the normal range. If it is out of range, please adjust the main power supply first.
b) Please contact after-sales service.
E8: Overflow fault
1) Description: The flowmeter or overflow switch is damaged.
2) Treatment method: please contact after-sales service.
E9: Abnormal wind pressure
1) Description: The high-efficiency filter is blocked by dust and needs to be replaced or the air pressure switch is damaged.
2) Treatment method:
a) Check whether the high-efficiency filter is full of dust, if so, please replace the filter directly.
b) If the high-efficiency filter is normal, replace the air pressure switch damaged.
E10: Abnormal intake of RO water (timeout)
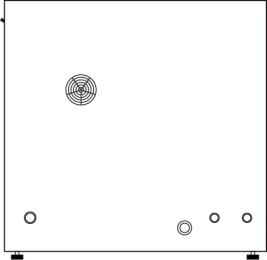
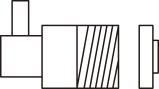
1) Description: The water intake time exceeds 10 min.
2) Treatment method:
a) Check whether the water source switch is turned on.
b) Check the filter screen of the inlet valve, pull the filter screen out of the inlet valve body, and check whether the filter screen is blocked.
c) All the above are normal, indicating that the water inlet valve or booster pump is damaged, please contact after-sales service.
E11: Abnormal intake of tap water (timeout)
1) Description: The water intake time exceeds 10 min.
2) Treatment method: check the tap water inlet valve in the same method as that of alarming E10.
E12: The door is not closed
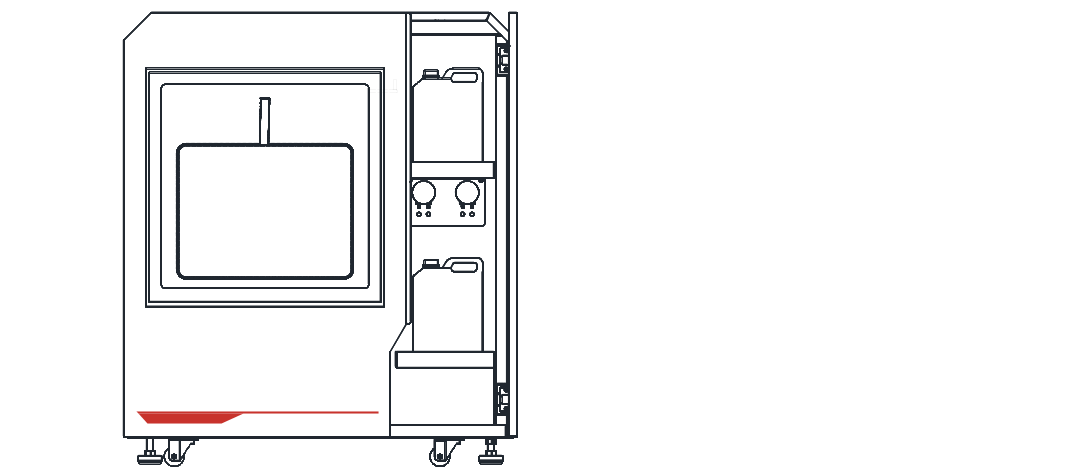
1) Description:
a) If the door is displayed in the closed state, it means that the door lock lever has not been pushed in place or the door sensor switch is damaged.
2) Treatment method: please contact after-sales service.
E13: Water leakage alarm
1) Description: There is water leakage inside the cleaning machine or the water leakage detection probe is damaged.
2) Treatment method:
a) Find the leakage point to solve the leaking situation, and clean the water on the leaking cable.
E13: Water leakage alarm
1) Description: There is water leakage inside the cleaning machine or the water leakage detection probe is damaged.
2) Treatment method:
a) Find the leakage point to solve the leaking situation, and clean the water on the leaking cable.
b) Replace the water leakage detection element.
E15: If the conductivity is not up to the standard, continue rinsing
Note: The conductivity of the water after cleaning is higher than the set value. The program will automatically perform a rinsing (RO) cleaning step until the conductivity is lower than the set value.
E16: The water level is too low
1) Description:
a) When the circulating pump is running, the water level in the cabin is lower than the set water level.
b) The water level switch is damaged
2) Treatment method:
1) Check whether the water level of the cabin is higher than the water level of the filter screen. If it is lower than the filter screen, check the filling water volume and whether there is water leakage in the pipeline.
2) Replace the water level switch
E17: There is water in the drying pipeline
1) Instruction:
a) Water enters the drying pipeline.
b) The float switch of the drying pipeline is damaged
2) Treatment method:
a) Remove the rear shell and open the drain valve to check whether water is discharged. If any water is discharged, it means that the DN50 electric ball valve is leaking and needs to be replaced;
b) If no water is discharged, check whether there is a problem with the float switch wiring here. If there is no problem with the wiring, the float switch is damaged and needs to be replaced.
8. Appendix
8.1 Program setting reference
1) Setting range of cleaning parametersName | Unit | Setting range | Description |
Dosage | ml | 0~999 | The volume of addition is 100ml every 60 seconds. |
(time) | min | 0~60 | * |
Cleaning temperature | ℃ | 0~100 | * |
Drying temperature | ℃ | 0~120 | Preferably set it below 70°C, as the temperature is too high and the temperature rises slowly. |
2) Cleaning program
Program name | Step | Step name | (time) (min) | Temperature (℃) | Water source | Dosage (ml) |
Quick washing | 1 | Cleaning with cleaning liquid | 10 | 60 | RO water | 80 |
2 | Cleaning with neutralizing liquid | 5 | 50 | RO water | 50 | |
3 | Rinsing | 2 | * | RO water | * | |
4 | Drying | 10 | 60 | * | * | |
Standard washing | 1 | Pre-cleaning | 2 | * | Tap water | * |
2 | Cleaning with cleaning liquid | 10 | 60 | RO water | 80 | |
3 | Cleaning with neutralizing liquid | 5 | 50 | RO water | 50 | |
4 | Rinsing | 2 | * | RO water | * | |
5 | Drying | 10 | 60 | * | * | |
Enhanced washing | 1 | Pre-cleaning | 2 | * | Tap water | * |
2 | Cleaning with cleaning liquid | 10 | 70 | RO water | 100 | |
3 | Cleaning with neutralizing liquid | 5 | 60 | RO water | 80 | |
4 | Cleaning with cleaning liquid | 10 | 70 | RO water | 80 | |
5 | Cleaning with neutralizing liquid | 5 | 50 | RO water | 50 | |
6 | Rinsing | 2 | * | RO water | * | |
7 | Drying | 10 | 60 | * | * | |
Custom | 1 | Pre-cleaning | 2 | * | Tap water | * |
2 | Pre-cleaning | 2 | * | Tap water | * | |
3 | Cleaning with cleaning liquid | 10 | 60 | RO water | 80 | |
4 | Cleaning with neutralizing liquid | 5 | 50 | RO water | 50 | |
5 | Cleaning with cleaning liquid | 10 | 60 | RO water | 80 | |
6 | Cleaning with neutralizing liquid | 5 | 50 | RO water | 50 | |
7 | Rinsing | 2 | * | RO water | * | |
8 | Rinsing | 2 | * | RO water | * | |
9 | Rinsing | 2 | * | RO water | * | |
10 | Drying | 10 | 60 | * | * | |
Oil washing | 1 | Pre-cleaning | 2 | * | Tap water | * |
2 | Cleaning with cleaning liquid | 10 | 60 | RO water | 80 | |
3 | Cleaning with neutralizing liquid | 5 | 50 | RO water | 50 | |
4 | Rinsing | 2 | * | RO water | * | |
5 | Rinsing | 2 | * | RO water | * | |
6 | Drying | 10 | 60 | * | * | |
Heavy oil washing | 1 | Cleaning with cleaning liquid | 10 | 70 | RO water | 80 |
2 | Cleaning with cleaning liquid | 10 | 70 | RO water | 80 | |
3 | Cleaning with neutralizing liquid | 5 | 50 | RO water | 50 | |
4 | Rinsing | 2 | * | RO water | * | |
5 | Rinsing | 2 | * | RO water | * | |
6 | Rinsing | 2 | * | RO water | * | |
7 | Drying | 10 | 60 | * | * | |
Organic washing | 1 | Rinsing with hot water | 2 | 60 | RO water | * |
2 | Cleaning with cleaning liquid | 10 | 70 | RO water | 80 | |
3 | Cleaning with neutralizing liquid | 5 | 50 | RO water | 50 | |
4 | Rinsing with hot water | 2 | 60 | RO water | * | |
5 | Rinsing with hot water | 2 | 60 | RO water | * | |
6 | Rinsing | 2 | * | RO water | * | |
7 | Drying | 10 | 60 | * | * | |
Inorganic washing | 1 | Cleaning with neutralizing liquid | 5 | 50 | RO water | 50 |
2 | Cleaning with cleaning liquid | 10 | 60 | RO water | 80 | |
3 | Cleaning with neutralizing liquid | 5 | 50 | RO water | 50 | |
4 | Rinsing | 2 | * | RO water | * | |
5 | Rinsing | 2 | * | RO water | * | |
6 | Rinsing | 2 | * | RO water | * | |
7 | Drying | 30 | 60 | * | * | |
Blood washing | 1 | Pre-cleaning | 2 | * | Tap water | * |
2 | Cleaning with cleaning liquid | 10 | 60 | RO water | 80 | |
3 | Cleaning with neutralizing liquid | 5 | 50 | RO water | 50 | |
4 | Rinsing | 2 | * | RO water | * | |
5 | Hot water disinfection | 2 | 60 | RO water | * | |
6 | Drying | 10 | 60 | * | * | |
Plastic washing | 1 | Pre-cleaning | 2 | * | Tap water | * |
2 | Cleaning with cleaning liquid | 10 | 60 | RO water | 80 | |
3 | Cleaning with neutralizing liquid | 5 | 50 | RO water | 50 | |
4 | Rinsing | 2 | * | RO water | * | |
5 | Rinsing | 2 | * | RO water | * | |
6 | Rinsing | 2 | * | RO water | * | |
7 | Drying | 10 | 60 | * | * | |
Glass washing | 1 | Cleaning with cleaning liquid | 10 | 60 | RO water | 80 |
2 | Cleaning with cleaning liquid | 10 | 60 | RO water | 80 | |
3 | Cleaning with neutralizing liquid | 5 | 50 | RO water | 50 | |
4 | Rinsing | 2 | * | RO water | * | |
5 | Rinsing | 2 | * | RO water | * | |
6 | Rinsing | 2 | * | RO water | * | |
7 | Drying | 10 | 60 | * | * | |
Rinsing | 1 | Rinsing | 3 | * | RO water | * |
2 | Drying | 10 | 60 | * | * |
Note: * means no set value.
8.2. Packing list
Number | Goods name | Unit | Quantity | Remarks |
1 | Cleaning machine host | Unit | 1 | |
2 | Cleaning rack | Unit | * | |
3 | Inlet pipe | Piece | 2 | |
4 | Drain pipe | Piece | 1 | |
5 | Liquid paraffin | Bottle | 1 | |
6 | Alkaline cleaning liquid | Barrel | 1 | |
7 | Acid cleaning liquid | Barrel | 1 | |
9 | Specification | Piece | 1 | |
10 | Drain pipe clip | Piece | 1 |