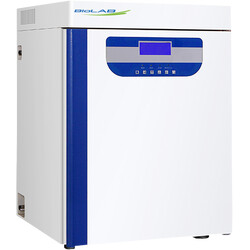
CO2 Incubator Air Jacketed BCAJ-201
- Sea, Air, Door to Door Shipping
- 1 Year Warranty
- US & European Standards
Designed to provide uniform temperatures and highly stable CO2 environment for your important cell cultures. UV light protects the cells from fungal contamination while HEPA provides clean air for optimal growth. Microprocessor avoids temperature fluctuation. Easy operation with data storage features, our product is a must have for cell culturing applications.
- Forced Convection
- Inner material: SUS304 stainless steel
- ALLHEATTM:Chamber Preheating Technology
- ALLFLOWTM:Clean Air Circulation System
Specification
Features
Applications
Capacity | 80 L |
Temperature Range | RT+5~55°C |
Ambient Temperature | 10~30°C |
Temperature Accuracy | 0.1°C |
Temperature Fluctuation | ±0.5 at 37°C |
Temperature Uniformity | ±0.8 at 37°C |
Temperature Recovery Time | (after 30 seconds door opening to 37°C) ≤ 8 min |
Ambient Humidity | <70% |
CO2 Range | 0~20% |
CO2 Sensor | IR sensor (±0.1%) |
CO2 Recovery Time | (after 30 seconds door opening to 5%) ≤2 min |
Filter | None |
Humidifying Method | Natural Evaporation |
Jacket Type | Water Jacketed |
Internal Dimension | 500Wx400Dx400H mm |
Exterior Dimension | 755Wx550Dx547H mm |
Shelves | 2 |
Weight | 35 kg |
Power | 500 W |
Power Supply | Single phase AC220V/50Hz |
- Forced Convection
- Inner material: SUS304 stainless steel
- ALLHEATTM:Chamber Preheating Technology
- ALLFLOWTM:Clean Air Circulation System
- ALLSENSTM:Programmable PID Controller
Cell Culturing, Tissue culturing, Tissue Engineering, Vitro fertilization, Mammalian cell research, Oncology studies.
Operating Manual for BCAJ-201

1. Safety notices and warnings
1.1 Safety operation and Preventive action
1.2 Safety operation and Preventive action
Safety operation and Preventive action
1.3 Instruction(application ,working principle, technical parameters)
1.4 Equipment installation
Equipment installation
2. Operation
2.3 Reservation
2.4 Running
2.5 Timing
2.6 Operation Stop
3 Sterilization function
3.1 UV sterilization
3.2 Damp-heat sterilization
3.3 High Temperature Sterilization
3.4 Alarm function
3.5 Temperature alarm
3.6 concentration alarm
3.7 Other alarms
3.8 Real-time curves
4 Menu interface
4.1 Mode selection
4.2 Fixed value pattern
4.3 Procedure model
4.3 Operational examples
5 History data
5.1 Interface description
5.2 Key Description
5.3 Export data
5.4 Interface description
5.5 key description
6. Parameter set
6.2 System set
6.3 Concentration & Humidity
6.4 Other set
6.5 User management
7. Alarm and security features
7.1 Routine using and maintenance
7.2 Optional using
8. Trouble shooting
8.1 Specification
8.2 Packing List
Notices
Ø In order to ensure safety to use this equipment, please read this manual carefully
Ø Make sure put this manual in convenient place for later use
Ø Our company doesn’t provide a safe guarantee if not use according to the instruction manual
Ø This manual only for user and authorized technician, please preserve it
Ø Not notice if any changes because of product improvement
Ø No right to copy this manual in without our company authorization
1. Safety notices and warnings
This manual has important use information , please comply.Make sure put this manual in convenient place for later use.
The symbols appear to the equipment and the manual, in order to you can safely and correctly operate this equipment ,avoiding the possible harm
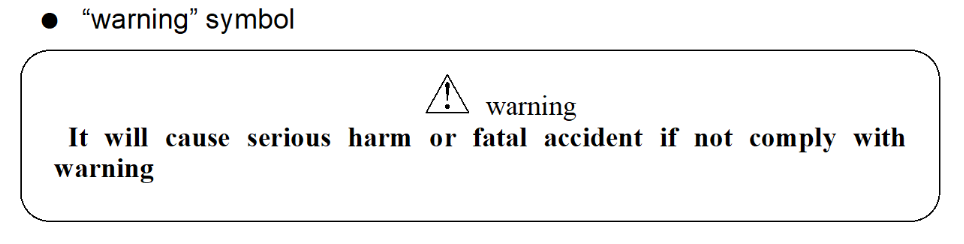
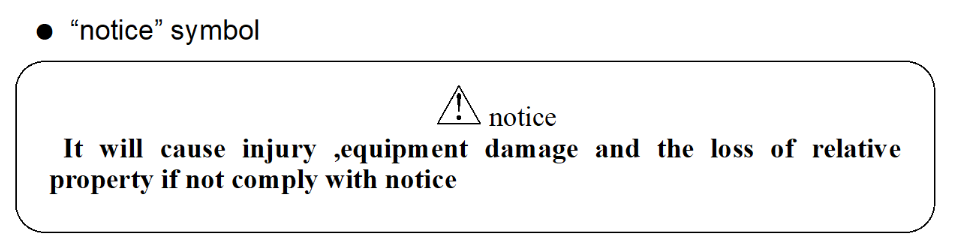
The meaning of symbols


Symbols in equipment





1.1 Safety operation and Preventive action
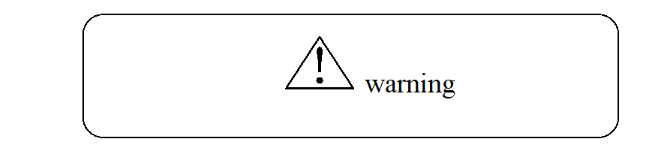














1.2 Safety operation and Preventive action
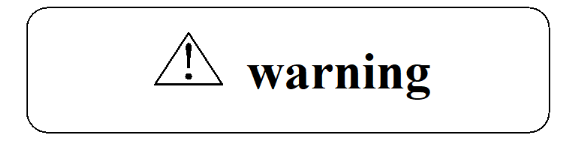












Safety operation and Preventive action
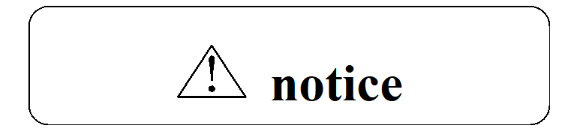








1.3 Instruction(application ,working principle, technical parameters)
ApplicationSeries BCAJ-200 series carbon dioxide incubator is an advanced instrument for cell, tissue and bacterial culture, which is a key equipment necessary for immunology, oncology, genetics and bioengineering. Used in microbiology, medicine, pharmaceutical, environmental protection, food, animal husbandry and other scientific fields of research and production. It is an artificial environment for the growth and reproduction of microorganisms and cells, bacteria and viruses caused by artificial methods in the incubator, such as controlling a certain temperature, humidity, gas, etc., mainly used for tissue culture and the culture of some special microorganisms.
Compared with the water jacket type, the air jacket type has the characteristics of fast heating and rapid temperature recovery than the water jacket type incubator, which is especially conducive to short-term culture and the culture requiring frequent opening and closing of the box door.
Performance
The carbon dioxide incubator is improved on the basis of ordinary culture, mainly to add CO2 and humidity to meet the environment required for the culture of microorganisms.
Control of carbon dioxide gas concentration. It's done with a carbon dioxide concentration sensor. The carbon dioxide sensor is used to detect the concentration of carbon dioxide in the box, the test results are transmitted to the control circuit and the solenoid valve and other control devices, if the concentration of carbon dioxide in the box is detected to be low, the solenoid valve is opened, and the carbon dioxide enters the box until the concentration of carbon dioxide reaches the set concentration, at this time the solenoid valve is closed, the carbon dioxide in the box is cut off, and the stable state is reached.
The equipment is an air jacket type heating, the principle is through the carbon fiber heating wire all over the outer wall of the box air jacket direct heating inside the box, also called six side direct heating
Technical parameters
Main technical index
Model ![]() argument | BCAJ-201 | BCAJ-202 |
Temperature control range | RT+ 5℃~60℃ | |
Temperature fluctuation | ≤ ±0.5 ℃(37℃) | |
Temperature uniformity | ≤ ±0.8 ℃ | |
Temperature recovery time | (When the door is restored to 37 ℃ for 30 seconds) ≤ 8min | |
CO2 control range | 0~20% | |
CO2 concentration recovery time | (When the door is restored to 5% in 30 seconds) ≤ 1.2min | |
Working environment | Temperature10 ℃~30℃ humidity ≤70%RH | |
Electric source | AC 220V 50Hz | |
Input Power (VA) | 600 | 750 |
Studio size (mm) | 500×400×400 | 650×460×540 |
Overall dimensions (mm) | 755×550×547 | 905×610×687 |
Weight (kg) | 35 | 55 |
Structure
Components
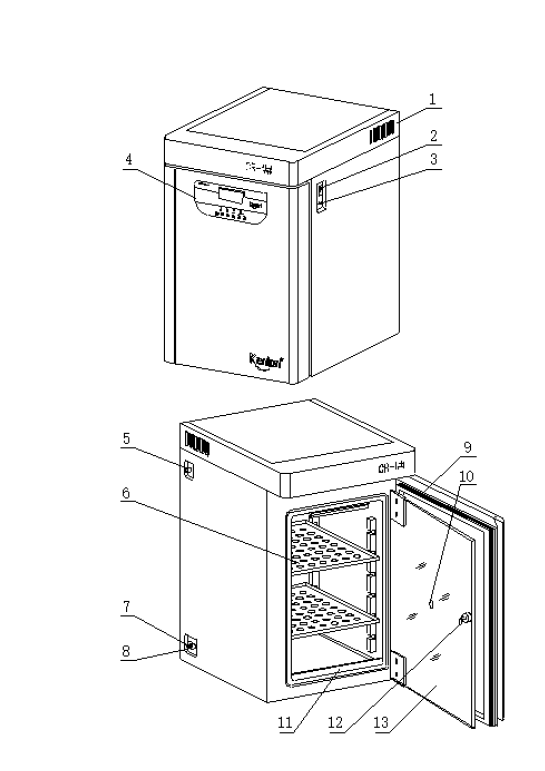
1.Power supply box 2.power switch 3.485 interface 4.Control panel
5.Water inlet 6.shelves 7.water outlet 8.overflow 9.Door seal magnetic strip
10. test hole 11.Weather bar 12.Glass door hook 13.Glass door
1.4 Equipment installation
Installation site
For proper operation and optimal performance, install the equipment in a location that meets the following conditions:

■ A location that is protected from direct sunlight.
Do not install the device in direct sunlight. Installation in direct sunlight may cause the device to fail to achieve the expected performance.
■ A location with adequate ventilation.
If the device is used in a small and closed room, it may not be able to dissipate heat in time, resulting in the device not working properly. The device must be at least 10CM away from the wall.
■ A location away from heat.
Avoid installing equipment near heat sources such as boilers or heaters. Excessive heat from the outside will affect the normal operation and control performance of the equipment.
■ A site with solid, level ground.
Install the device on a solid and level ground. An uneven ground or tilted device may cause device failure or injury. Install the equipm
equipment shaking and noise.
■ A location that is not prone to high humidity.
Install the device in a place where the humidity is no more than 70%. If installed in high humidity, it may cause leakage or electric shock.
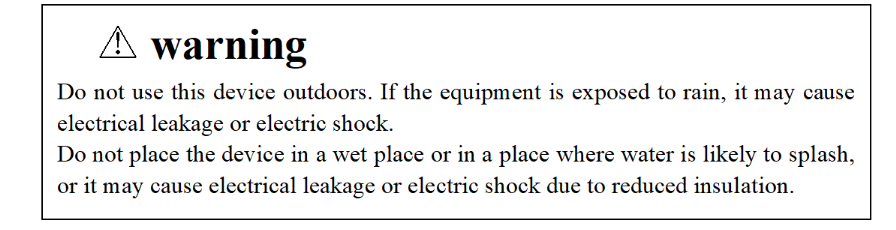
■ A location free of flammable or corrosive gases.
Do not install the equipment in a place with flammable or volatile substances, or it may cause an explosion or fire. Or it may cause leakage, electric shock or damage to the equipment due to corrosion.
Equipment installation
Installation1.Take off packing materials
Take off packing all materials ,open the door for ventilation . Please use neutral detergent to clean dirt if the shell and panel is dirty.then wipe with wet cloth and at last wipe-dry with dry cloth
2. balancing equipment
Before using the equipment, the equipment should be balanced due to uneven position to prevent the equipment from shaking and affecting the use.
3. Earthing
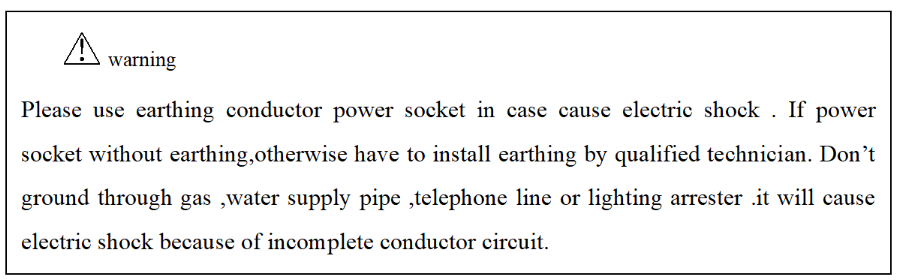
4. If idle equipment
Before idle ,Make sure the sink inside the box is drained of water then heat up to 55 and dry for two hours, open the door and cool completely.
5. Before move equipment
Before moving the equipment, if there are items on the carrier bracket in the box, they should be removed to prevent it from slipping.
Preparation before operation
Before starting the device for the first time, please follow the following procedures:
1. The magnetic outer door can be opened by turning to the right;
2. Turn the knob of the inner glass door clockwise by hand, and then turn it to the right to open the inner door;
3. Take out the shelf accessories inside the equipment, wipe the shelf and the inner wall of the box with gauze for cleaning;
4. Put the shelf into the equipment according to their own culture or experimental requirements;
5. If the items need to be placed on the same shelf, leave space between each other to facilitate the cultivation of items;
6. The carbon dioxide special pressure reducing valve is installed on the carbon dioxide cylinder, the joint shall not have gas leakage phenomenon, the pressure reducing valve output joint is connected with the rubber hose provided by the factory with inner diameter 8, pressure 0.2Mpa and the equipment box back marked with "CO2" air inlet connector, and the compression ring is fixed, no gas leakage, carbon dioxide cylinder is not opened temporarily.
7. Connect the device according to the figure. After the preceding steps are complete, the device is in use.
8. Insert the water supply pipe according to the figure, fill the water tank with clean water, place it on the top of the tank, and connect it with the water supply pipe.

2. Operation
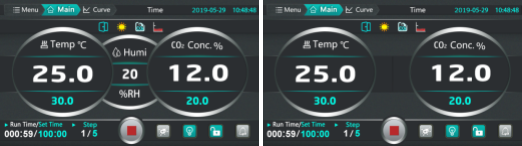
2.1 Key Description
Icon | Name | Description |
![]() | [Start] | Click the pop-up dialog box to make the system run; |
![]() | [Stop] | Click the pop-up dialog box to make the system stop; |
![]() | [Catalogue] | Click to enter the directory interface; |
![]() | [Curve] | Click to enter the real-time curve interface; |
![]() | [Sterilization set] | In the running stop state, click on the sterilization setting key, will enter the sterilization setting interface; |
![]() | [Lighting] | Turn on or off lighting; |
![]() | [Mode set] | Click Enter Mode Set interface |
![]() | [Real time] | Click to enter the real-time modification interface; |
![]() | [Alarm] | When there is an alarm, the icon flashes red; Click to enter the alarm record interface; |
![]() | [Lock] | Click to enter the lock screen interface; |
2.2 Operational status
The four running states of the system are displayed above the main interface, namely [stop],[ reservation waiting ],[ running] and [timing];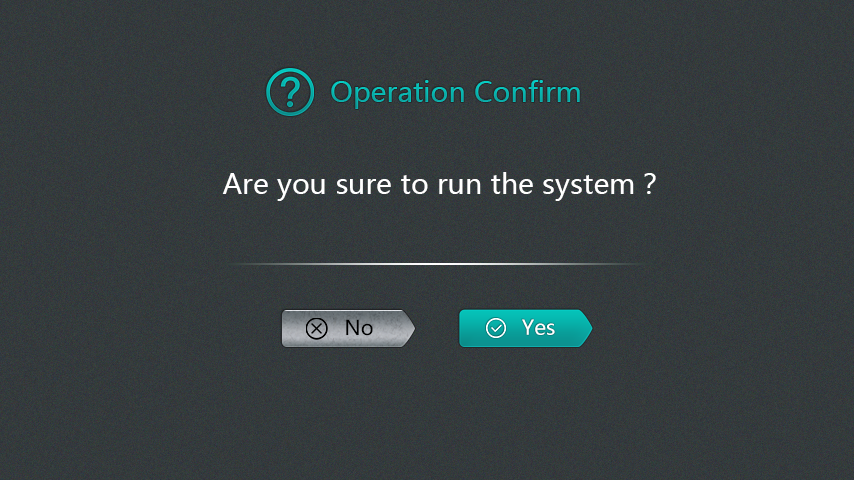
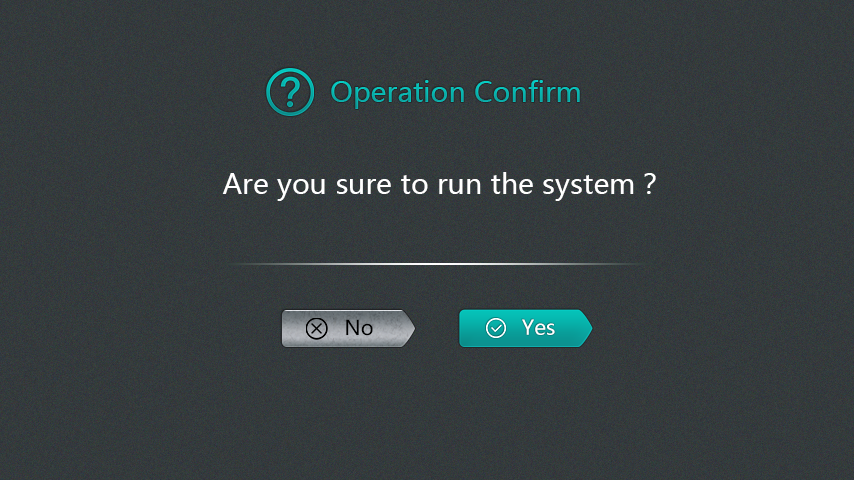
2.3 Reservation
At the [parameter set]->[time parameter] interface, the user can set the reservation time, if the reservation time is greater than the current time, in the [monitor interface], click the [run] key, the system will first enter the [reservation waiting] state; when the system time reaches the reservation time, the system automatically enters the [running] state;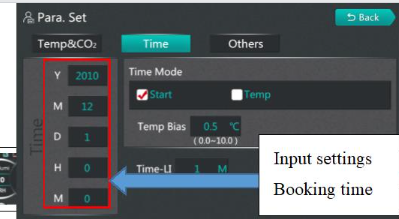
2.4 Running
When the system time reaches the reservation setting time, the system enters the [running] state from the [reservation waiting] state, or the user does not set the reservation time, then click the [running] key system to enter the [running] state directly. At this time, the system will be selected;A user can set [select] in the [parameter set]->[time parameter] interface, as shown in the following figure:
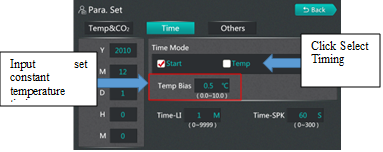
- Start time: the system directly skipped the [running] state, directly into the [in] state;
- Thermostatic timing: when "set temperature-therm timing deviation value ≤ temperature measurement value ≤ set temperature + constant temperature timing deviation value ", the system from [running] state, into [middle] state;
2.5 Timing
When the condition of timing judgment is satisfied, the system enters the [middle] state from [running], and the timing time begins to change. According to different control mode and mode conditions (reference mode setting), the system automatically converts in [running] and [middle] states. When the running stop condition is satisfied, enter the [stop] state;2.6 Operation Stop
After the running time is over, the system closes all outputs and enters the stop state;3 Sterilization function
Users can choose sterilization methods in [system set]->[ temperature & sterilization parameters]. There are three sterilization methods: ultraviolet sterilization, humid heat sterilization and high temperature sterilization. Click the sterilization icon to enter the sterilization password interface at the monitoring interface and enter password 1 into the sterilization interface.3.1 UV sterilization
Use ultraviolet lamp to sterilize, after the user opens sterilization, sterilization relay closes, sterilization lamp opens.3.2 Damp-heat sterilization
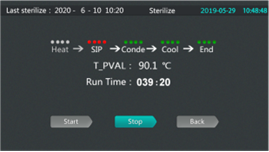
A total of 5 stages of damp-heat sterilization:
1) heating stage: heating until 90.0℃, heating tube open ,90.0℃ after jumping to disinfection stage;
2) disinfection stage: maintain 90.0℃,6 hours long, heating tube open;
3) condensation stage: maintain 90.0℃,10 hours, bottom heating pipe closed;
4) cooling stage: when the temperature drops to 37.0℃, jump to the end stage, the bottom heating pipe is closed;
5) end stage: the whole process of damp-heat sterilization is completed.
3.3 High Temperature Sterilization
High temperature sterilization, high temperature sterilization temperature can be set in [system setting ]->[ temperature] sterilization parameters.3.4 Alarm function
When an alarm occurs in the system, the buzzer calls and prompts, and the [alarm] button surface in the monitoring interface is red flashing. Click to enter the alarm list interface to view the latest 20 alarm contents, as shown in figure: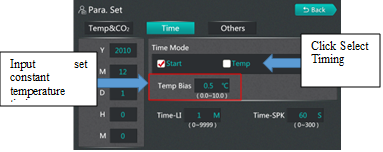
3.5 Temperature alarm
Temperature alarm includes [main temperature overflow ][ door temperature overflow ][ main temperature over-temperature ][ main temperature under temperature ][ door temperature over-temperature] five types, as follows:Alarm type | Alarm Description |
Main temperature overflow | When the temperature of the main temperature sensor fails, the main temperature overflow alarm is generated, the system stops running, and the buzzer calls (click on any interface to mute); |
Door temperature overflow | When the temperature of the door temperature sensor fails, the door temperature overflow alarm is generated, the system stops running, and the buzzer calls (click on any interface to mute); |
Over temperature of main temperature | When "main temperature measurement value > main temperature setting value + over temperature alarm deviation ", there is a main temperature over temperature alarm, buzzer calls (click on any interface to mute), cut off the main temperature heating circuit; |
Main temperature | When "under-temperature alarm deviation" is zero, no main temperature under-temperature alarm; When "main temperature measurement value < main temperature setting value + under temperature alarm deviation ", there is main temperature under temperature alarm, buzzer calls (click on any interface to mute); |
Door temperature over temperature | When "door temperature measurement value > door temperature setting value + door temperature over temperature alarm deviation ", there is door temperature over temperature alarm, buzzer calls (click on any interface can be silenced), cut off the door temperature heating circuit; |
The user can set the value of [over temperature alarm deviation ][under temperature alarm deviation] in [user set]->[temperature & sterilization parameter], and set the value of [door temperature over temperature alarm] in [system setting ]-[ temperature & sterilization parameter] in [system setting ]-;
3.6 concentration alarm
Concentration alarms include three types of [concentration overflow ][ over concentration ][ under concentration], as follows:
Alarm type | Alarm Description |
Main temperature overflow | When the temperature of the main temperature sensor fails, the main temperature overflow alarm is generated, the system stops running, and the buzzer calls (click on any interface to mute); |
Door temperature overflow | When the temperature of the door temperature sensor fails, the door temperature overflow alarm is generated, the system stops running, and the buzzer calls (click on any interface to mute); |
Over temperature of main temperature | When "main temperature measurement value > main temperature setting value + over temperature alarm deviation ", there is a main temperature over temperature alarm, buzzer calls (click on any interface to mute), cut off the main temperature heating circuit; |
Main temperature | When "under-temperature alarm deviation" is zero, no main temperature under-temperature alarm; When "main temperature measurement value < main temperature setting value + under temperature alarm deviation ", there is main temperature under temperature alarm, buzzer calls (click on any interface to mute); |
Door temperature over temperature | When "door temperature measurement value > door temperature setting value + door temperature over temperature alarm deviation ", there is door temperature over temperature alarm, buzzer calls (click on any interface can be silenced), cut off the door temperature heating circuit; |
The user can set the value of [over temperature alarm deviation ][under temperature alarm deviation] in [user set]->[temperature & sterilization parameter], and set the value of [door temperature over temperature alarm] in [system setting ]-[ temperature & sterilization parameter] in [system setting ]-;
3.7 Other alarms
Concentration alarms include three types of [concentration overflow ][ over concentration ][ under concentration], as follows:Alarm type | Alarm Description |
Low water level alarm | Detect low water level switch quantity, stop running, buzzer calls (click on any interface to mute); |
Gated alarm | In the running state, the continuous opening time exceeds the door alarm delay time, there is a gated alarm, buzzer calls (click on any interface can be silenced); |
Communication alarm | The communication between the current computer and the touch screen is blocked for more than 20 seconds, and there is a communication fault alarm |
3.8 Real-time curves
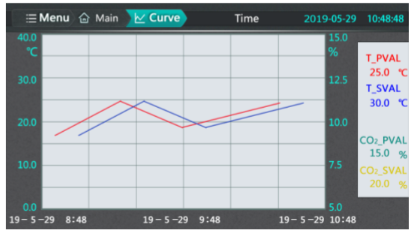
The user can click on [curve] or slide the screen to the left to enter the [real-time curve] interface. In the real-time curve interface, the temperature and speed curves can be viewed in the last 2 hours. The vertical coordinate range is 20.0℃ and 5.0;
4 Menu interface
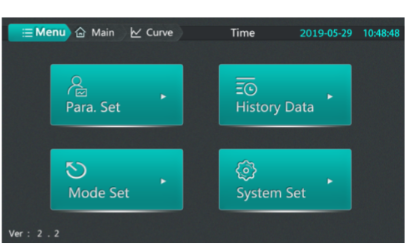
Users can access the [parameter set],[history data ],[mode set],[system set] interfaces in the menu interface; the version number of the upper and lower computers can be viewed in the lower left corner (version :2.2, the first value is the control board version number, the second value is the touch screen version number)
4.1 Mode selection
There are two ways to enter the mode setting interface :1, in the monitoring interface click on the set value to enter the mode setting interface quickly ;2, in the [menu interface] click on the "mode setting" to enter the mode setting interface;The system has two control modes: fixed value mode and program mode; A user can edit the number of segments in each mode (1~5), and time (0~999:59), temperature (according to [system set]–" temperature setting upper limit "in >[temperature & sterilization] determines setting range), concentration (0.0~20.0%));
4.2 Fixed value pattern
According to the choice of timing mode in [user set]->[time parameter] and whether the time setting value is 0, the following working mode can be realized:Time set value | Timing | Description |
0 | —— | Timing time is always 0, continuous operation does not stop; |
Not 0 | Start time | Click on the running system to start timing, timing time to set time, stop running; |
Constant temperature timing | Click on the operating system to control the temperature and concentration, after reaching the range of constant temperature timing start timing, timing time to the set time, stop running; |
4.3 Procedure model
In program mode, multiple temperature, concentration control steps and control time of each step can be set;
Time set value | Timing | Description |
0 | Running time | Step time is not timed, the system directly jump to the next set value to continue running, if the last paragraph, the operation stops; |
Constant temperature timing | Step time is not timed, the system controls the temperature and concentration, after reaching the constant temperature timing range, jump to the next set value to continue to run, if the last section, the operation stops; | |
Not0 | Running time | Click run, step time start timing, step time to set time, jump to the next set value to continue running, step time to start the timing again, if the last paragraph, the operation stops; |
Constant temperature timing | Click on the operation, the system controls the temperature and concentration, after reaching the constant temperature timing range, the step time begins to time, after the step time reaches the set time, jump to the next set value to continue to run, The temperature still needs to reach the constant temperature range after the step time starts again, if the last paragraph, the operation stops; |
4.3 Operational examples
Fixed value mode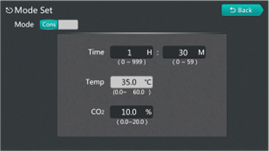
For example: set temperature 35.0℃, set concentration 10.0%, run 1 hour 30 minutes, set the operation flow as follows: in [monitor interface] click the set value to enter [mode setting] interface (when the current running mode is fixed mode, directly enter [fixed mode] setting interface; when the current running mode is program mode, enter [program mode] setting interface, then click mode selection button to enter [fixed mode] setting interface), after setting the correct set value in [fixed mode] setting interface, click return, if the current mode is not fixed mode, will prompt whether to modify the mode, and then click [confirm] to complete the determination of fixed value mode;
No. number | Content | Description |
1 | Time set | Click the Time Textbox (Time: Points) to set to 1:30 |
2 | Temperature set | Click to set the set value mode to set the temperature value |
3 | Concentration set | Click to set the set value mode to set the concentration value |
Programmatic pattern
When the temperature rises to 25.0±0.5℃ for 1 hour and 30 minutes, then to 35.0℃ for 1 hour, set as follows:
Number of steps | Set time | Set temperature | Set concentration |
Paragraph 01 | 1.30(1 hour 30 minutes) | 25.0℃ | 10.0% |
Paragraph 02 | 1:00(1 hour and 0 minutes) | 35.0℃ | 12.0% |
Action flow as follows- determine [user set] [time parameters] timing mode selection [constant temperature]; in [monitor interface] click on the set value to enter the [mode set] interface (when the current running mode is program mode, Go directly to the program mode setting interface; When the current running mode is fixed mode, enter the [fixed mode] setting interface, then click the mode selection button to enter the [program mode] setting interface), after setting the correct setting value in the [program mode] setting interface, click return, If the current mode is not program mode, you will be prompted to modify the mode, and then click confirm to complete the program mode determination, such as the following figure:
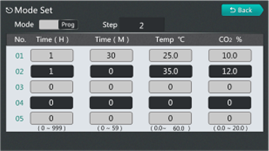
No. | Content | Description |
1 | Paragraph set | Click on the text box, pop up the numeric keyboard, set to 2 |
2 | Time set | Click 01 and 02 time boxes respectively to set 1:30 and 1:00 |
3 | Temperature set | Click on section 01 and section 02 temperature text boxes to set to 25.0 and 35.0 |
4 | Concentration set | Click on the 01 and 02 concentration text boxes to set to 10.0 and 12.0, respectively |
5 History data
5.1 Interface description
The user enters the [history data] interface, can view the system automatically saved temperature measurement, set value, concentration measurement, set value, humidity measurement value and running, alarm state of historical data, save interval can be set;
5.2 Key Description
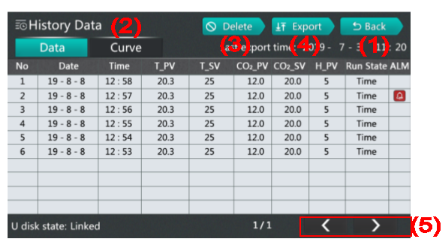
No. number | Content | Description |
1 | [Return] Key | Click to return to [Directory Interface]; |
2 | [History Curve] Key | Click to enter the history curve interface; |
3 | [Data Delete] Key | Click the pop-up Clear Data Confirmation dialog box; click Yes to delete the data |
4 | [Data Export] Key | U the disk is connected, click the data export button to pop up the export data confirmation dialog box, and then click Yes to export the data |
5 | [Up ][ Next page] key | Click to view historical data on the previous or next page; |
5.3 Export data
Users need to export historical data with U disk, can click on the [export] button, pop up to confirm whether to export dialog box, the user should confirm that the U disk has been inserted, to avoid system errors, click OK to complete the data guide operation as shown below;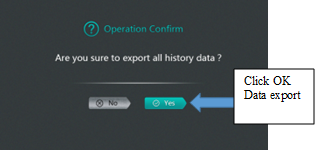
5.4 Interface description
In the history curve interface, the user can view the trend of the historical data curve for a period of time, which corresponds to the data stored in the history data.
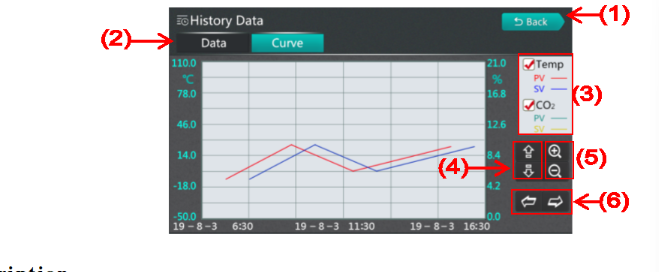
5.5 key description
No. | Content | Description |
1 | [Return] Key | Click to return to the directory interface |
2 | [Historical Data] button | Click to enter the History Data interface |
3 | Does the temperature and concentration curve show | Click to set the temperature curve and concentration curve respectively |
4 | Upward and downward curves | Click on the vertical coordinates of the up or down curves |
5 | Zoom in and narrow the curve | Click on the zoom or zoom curve |
6 | Left shift, right shift | Click the left or right curve |
6. Parameter set
Under the permission of the administrator and the tester, you can enter the [ parameter setting] through the [menu interface].Temperature & concentration
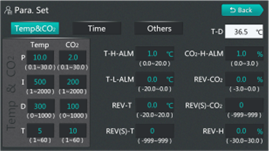
Time parameters
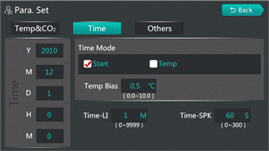
Name | Function | Initial value (set range) |
Booking time | Year, month, day, hour, minute When the current time is less than that time, the system enters the reservation waiting state until the current time is greater than or equal to that time, and the system enters the running state; When the current time at startup is greater than or equal to that time, the system enters the running state; | 1 December 2010 |
Time Mode | Start time: from the running state can directly jump into the timing state; Constant temperature timing: when the system is in operation, and when "main temperature setting value-therm timing deviation ≤ main temperature measurement value ≤ main temperature setting value + constant temperature timing deviation ", the system can enter the timing state; | Start time |
Constant temperature timing Deviation (Temp Bias) | Within this parameter, the system enters the "timing" state from the "running" state and starts the timing. | (0~10.0℃) 0.5 |
End of operation Prompt time (Time-SPK) | Buzzing prompt time after running. Note :0 means continuous call. | (0~300 s)60 |
Lighting time (Time LI) | After the lighting is turned on, the lighting time is automatically turned off.(Lighting function can be set in system settings) Note :0 means that the lighting must be manually turned off. | (0~9999 min)1 |
Other parameters
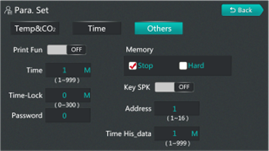
Name | Function | Initial value (set range) |
Print function | Off: Print function is off On: Print function is on | Closed |
Print interval | Every time this parameter is timed, print out, current temperature measurement, temperature setting, concentration measurement, concentration setting Print header and current date for the first time or whenever the date changes | (1~999 min)1 |
Lock time | Automatic lock screen time 0 time no automatic lock screen. | (0~300 min) 0 |
Lock screen password | When the lock screen time is 0, click the unlock key to enter the monitor interface directly | 0 |
Button | Touch the touch screen with a buzzer | Closed |
Power down Mode of operation (Memory) | Do not start: after boot state is stopped state; Hard start: when the system is non-stop before power down, turn on again to run state, otherwise it is stop state; | Not started |
Address | Local address. | (1~16)1 |
Data recording interval (Time His_data) | Interval of historical data storage | (1~999 min)1 |
6.2 System set
Enter [system set], you need to enter password 9 to enter, otherwise pop up error prompt dialog box;
Temperature & Sterilization
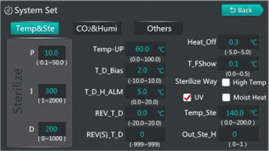
Name | Function | Initial value (set range) |
sterilization ratioP | Time ratio regulation. | (0.1~50.0) 10.0 |
sterilization integral I | Integral action regulation. | (1~2000 s)300 |
Differential D of sterilization | Differential action regulation. | (0~1000 s)200 |
Temperature Set upper limit (Temp-UP) | The maximum value of a temperature set value. | (0~100.0℃) 60.0 |
Heating Turnoff Deviation (Heat-Off) | Turn off the heating output when [temperature measurement value ≥ temperature setting value + heating turn off deviation]; and | (-5.0~5.0℃) 0.3 |
Temperature insensitive zone (T-FShow) | Insensitive areas of main and gate temperatures | (0.0~0.5℃) 0.1 |
Door temperature Set deviation (T-D-Bias) | Door temperature setting value =(main temperature) temperature setting value + door temperature setting deviation value | (-10.0~10.0℃) 2.0 |
Door temperature Over temperature alarm AH (T-D-H-ALM) | When [door temperature measurement value >(door temperature setting value +AH)], there is door temperature over temperature alarm | (0.0~20.0℃) 5.0 |
Door temperature Deviation correction (REV-T-D) | Usually used to correct errors in low temperature measurements. Deviation value = actual temperature value - current measurement value | (-20.0~20.0℃) 0.0 |
Door temperature Slope modification (REV(S)-T-D) | It is usually used to correct the error caused by high temperature measurement. Slope value =1000*(actual temperature-gate temperature measurement)/gate temperature measurement | (-999~999) 0 |
Method of sterilization | 1: UV sterilization ;2: Wet heat sterilization ;3: High temperature sterilization | UV sterilization |
High temperature Sterilization temperature (Temp-Ste) | The sterilization method is the setting value of sterilization temperature during high temperature sterilization | (0.0~200.0℃) 140.0 |
High temperature sterilization output (Out-Ste-H) | When the sterilization mode is high temperature sterilization, when the output of high temperature sterilization is 0, the output of sterilization is the main temperature heating, and when the output of high temperature sterilization is 1, the output of sterilization is the output of sterilizing relay | (0~2) 0 |
6.3 Concentration & Humidity
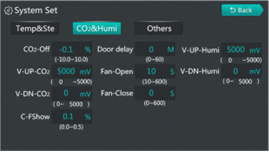
Name | Function | Initial value (set range) |
Inflatable Turnoff (CO2-Off) | When [concentration measurement value ≥ concentration setting value + inflatable turn off deviation], turn off the inflatable relay output. | (-5.0~5.0%)-0.1% |
Concentration Voltage ceiling (V-UP-CO2) | Maximum output voltage signal of concentration sensor | (Concentration Voltage Limit ~5000)5000 |
Concentration Lower voltage (V-DN-CO2) | Minimum output voltage signal of concentration sensor | (0~ concentration voltage upper limit)0 |
Insensitive concentration zone (C-FShow) | Insensitive areas of concentration measurements | (0.0~0.5℃) 0.1 |
Door Alarm Delay (Door Delay) | When the gating is opened, after waiting for the delay time of the door alarm, the gating alarm is triggered. This value is set to 0 when the function is invalid, no gated alarm. | (0~60 min)0 |
Fan opening time (Fan-Open) | When the temperature measurement value reaches the set value (SP-0.3℃≤PV≤SP+0.3℃) and lasts for 5 minutes, the fan can be set to open or close intermittently. In seconds. Go beyond this range and continue | (20~600s)60 |
Wind time (Fan-Close) | Work with fan opening time, when this value is set to 0, the fan continues to run. | (0~600s)0 |
Humidity voltage upper limit (V-UP-Humi) | Maximum output voltage signal of humidity sensor | (Humidity Voltage Limit ~5000)5000 |
Lower limit of humidity voltage (V-DN-Humi) | Minimum output voltage signal of humidity sensor | (0~ humidity voltage upper limit)0 |
Low water signal | Normally open: low water level alarm when the low water level signal is disconnected; Normally closed: low water level alarm when the low water level signal is closed; | Normally open |
6.4 Other set
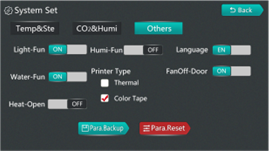
Name | Function | Initial value (set range) |
Lighting function | Close: monitor interface without lighting button; Open: monitor interface without lighting button; | Open |
Water level function | Closed: no low water level detection; Open: low water level detection; | Open |
Open door heating | Open door heating and closing: the door alarm is monitored in operation, the controller stops heating output; after the door is closed, the controller automatically maintains for 2 minutes and continues to heat the output; Open door heating open: in operation monitoring door alarm, the controller can continue to heat the output; | Closed |
Humidity display | Humidity display: do not display humidity measurements at the monitoring interface; Humidity display: display humidity measurement value in monitoring interface; | Closed |
Printer model | Type of printer used | Ribbon printer |
Language display | Display in Chinese or English | Chinese Display |
Open door fan | Is the fan closed when the door opens | Open |
Auto-tuning temperature | Auto-tuning setting temperature | (0.0 ~ 100.0 ℃ ) 60.0 |
Auto-tuning | Auto-tuning open/closed | |
User management | Three-level user rights management | |
Save factory values | Save factory values | |
Restore Factory Defaults | Restore factory values |
6.5 User management
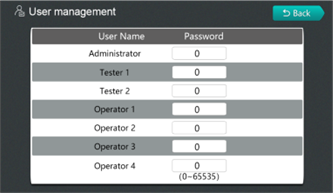
The user can enter[User Management] to set the user's password with three levels of authority. The user with administrator authority has all authorities except for system settings. The user with tester authority can select modes and set parameters. The operator authority can only access historical data.
7. Alarm and security features
- Temperature sensor fault alarm: The screen displays: -- words, indicating that the temperature sensor or controller itself is faulty.- Temperature upper limit alarm: When the measuring temperature exceeds the set temperature by 1 degree, the heating will stop working, and the instrument alarm lamp will light up and the alarm sound will ring continuously.
7.1 Routine using and maintenance












7.2 Optional using
RS-232/RS-485 instructions for use of the converter
- In order to proceed with data communication between the different standard serial interface to the computer, an external device or smart instrument, must provide conversion of standard serial interface. The converter is compatible with RS-232, RS-485 standard, capable of converting single-ended RS-232 signal to a balanced differential RS-485 signals.(it can connect 16 controller of this series together at the same time)
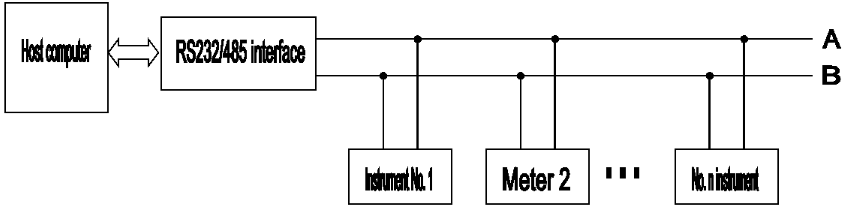
Trouble shooting
- Data communication failure
(1)Check if RS-232 port inside connection is correct.
(2)Check if RS-485 port inside connection is correct.
(3)Check if port is connected.
- Data is missing or incorrect
Please check if data communication equipment rate and format is accordance.
8. Trouble shooting
Trouble shooting | handling |
Sensor fault indication (- - -) | ·The temperature sensor is abnormal. Check whether the temperature sensor is in good condition. Model PT100。 |
The temperature does not rise to the set value | ·Check whether the display is heated. If it is heated, the electric heating wire is damaged or the control board or circuit is faulty. |
Slow temperature rise | ·Open the outer door to check whether the fan in the box is running. If the fan is not running, check the fault according to the wiring diagram. |
CO2 concentration does not reach the set value | ·Whether the external CO2 gas cylinder valve is opened and the CO2 gas cylinder pressure is normal (not less than 3Kg); · The intake control solenoid valve is faulty. Please check the fault according to the wiring diagram |
No display | · Check whether the incoming plug wire has AC220V; · Check whether the power switch is on; · Check whether the power switch of the equipment is tripping. If it is tripping, please check the fault according to the wiring diagram. |
8.1 Specification
Name | ;name; | |
Model | BCAJ-201 | BCAJ-202 |
Exterior Dimension (H * W * D) | 755×550×547 | 905×610×687 |
Interior Dimension (H * W * D) | 500×400×400 | 650×460×540 |
Effective volume | 80L | 160L |
Input power | 500W | 650W |
Shell | Cold-roll steel sheets with powder coat treatment | |
Inner shell | SUS304 mirror stainless steel | |
Door | Self-priming door seal insulation design | |
Shelf | High quality SUS304 mirror stainless steel plate, adjustable height position; | |
Heating preservation system | Imported environmental protection material filling | |
Temperature control system | PID system self-tuning program | |
Heating system | New carbon fiber three-dimensional heating method | |
Air valve | Brand imported solenoid valve | |
Temperature sensor | Samsung temperature sensor PT100 | |
Display | LCD screen; | |
CO2 sensor | Imported original infrared sensor | |
Alarm system | Temperature overtemperature alarm, temperature sensor fault alarm,CO2 excessive alarm and sound and light prompt; | |
Weight | 35Kg | 55Kg |
Shelf(standard) | Two pieces | Three pieces |
Optional parts | 485/232 conversion port, integrated printer, gas interface, monitoring software. |

Wiring diagram
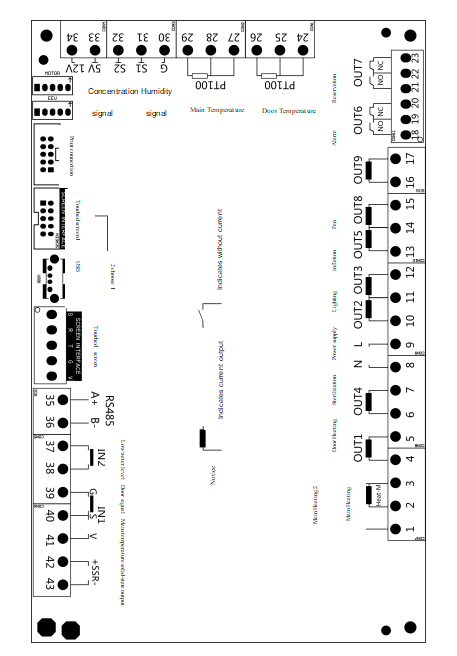
8.2 Packing List
No. | Name | Quantity | Note |
1 | Finish product | 1 | |
2 | instruction manual | 1 | |
3 | Certificate of conformity | 1 | |
4 | shelf | 80L/2 pieces 、 160L/3 pieces | |
5 | Feed water tray | 1 | |
6 | Gas pipe | 2 meters | |
7 | Charging pipe | 1 | |
8 | Power cord | 1 | |
9 | water tank | 1 | 300mm long water pipe |
10 | relief valve | 1 |