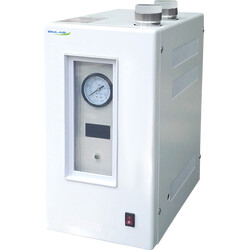
Automatic Hydrogen Generator BGEN-303
- Sea, Air, Door to Door Shipping
- 1 Year Warranty
- US & European Standards
Engineered to provide a safe, ultrahigh-purity alternative to high-pressure gas cylinders in the laboratory for carrier and fuel gas applications, most often in gas chromatography. It is compact, reliable, practical and cost-effective alternative to pressurized cylinders. Due to hydrogen’s flammability, the importance of safety features is paramount.
- Automatic control, constant pressure, constant flow
- Membrane separation technique
- Deoxidation and dehydration device, high purity
- Compact, frees up valuable space
Specification
Features
Applications
Hydrogen purity | 100.00% |
Flow Rate | 0-300 ml / min |
Output Pressure | 0-0.4 Mpa |
Pressure Stability | <0.001 Mpa |
Dimension | 370x330x180 mm |
Net Weight | 10 kg |
Consumption Power | 150 W |
Power Supply | 220 V±10%, 50 Hz |
- Automatic control, constant pressure, constant flow
- Membrane separation technique
- Deoxidation and dehydration device, high purity
- Compact, frees up valuable space
- Easy operation, eliminate the need for expensive gas cylinder
- Safe and reliable
Gas quality monitoring, General laboratory, Gas chromatography, TOC, Industries, Environmental, Petrochemical, Pharmaceutical, Cinical, Forensics.
Operating Manual for BGEN-303

1. INTRODUCTION
2. DESCRIPTIONS FOR EACH PART OF INSTRUMENT
3. INSTALLATION AND OPERATION
3.1 Preparation before the operation
3.2 Self checking of instrument (Never connect with gas chromatograph)
3.3 Operation of instrument (Connect with the gas chromatograph)
4. WORKING PRINCIPLE AND FEATURES OF INSTRUMENT
4.1 Working principle:
4.2 Features of instrument
5. TROUBLING SHOOTING
6. MAIN TECHNICAL PARAMETERS
7. Packing list
1. INTRODUCTION
BGEN-303 High Purity Hydrogen Generator employs the latest technology to satisfy various models of gas chromatographs, which are manufactured by domestic and aboard manufactures.Its pressure control adopts high sensitive fuzzy control and automatic tracking system to make the precision range of the pressure stability less 0.001MPa. There are two different output pressures setting according to the requirements of different gas chromatographs and detectors such as: “L” status and “H” status. “L” status shows 4Kg/cm2 (about 0.4MPa). “H” status shows 6Kg/cm2 (about 0.6MPa). When using the hydrogen as the carrier gas, such as TCD, set the pressure to “H” status for obtaining the stable flow and sufficient pressure. When using the hydrogen as the combustion gas, such as FID, set the pressure to “L” status. It not only makes stable hydrogen pressure and flow, but also extends the lifetime of the instrument.
Its electrolytic cell utilizes transient metal element catalytic technology and process multi-stage purification. There are two filters providing with the instrument. The hydrogen purity can be reached up to: oxygen content : less 3PPM, water content dew point temperature :-56℃.
2. DESCRIPTIONS FOR EACH PART OF INSTRUMENT
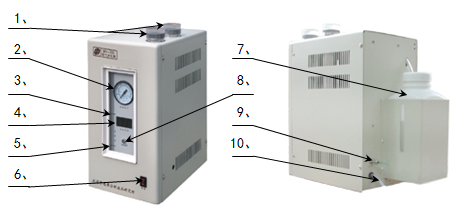
Front panel Rear panel
1-- Purified tube 6-- Switch of power supply
2-- Indicator of working pressure 7-- Liquid bucket of electrolytic solution
3-- Upper limit indication of electrolytic solution 8-- Indicating lamp of electrolytic solution
4-- Hydrogen digital flow indicator 9-- Outlet port of hydrogen
5-- Low limit indication of electrolytic solution 10-- Cable of power supply
3. INSTALLATION AND OPERATION
3.1 Preparation before the operation
3.1.1 Take the instrument out from the packing box. Check if there is any damage on the instrument during the transportation and verify that all of spare parts are provided with the main unit according to the packing list.
3.1.2 Adding the electrolytic solution
1) Take out the potassium hydroxide (200g) from the spare parts and put them all into a container, then add secondary distilled water or de-ionized water of 500ml as the master solution and fully mixes it. Use it after the electrolytic solution cooling down.
2) Open the outer cover of the liquid bucket of the instrument, take out the cotton from it.
NOTE: The cotton is mainly used to avoid the liquid leakage during the transportation. It must be taken out during running.
3) Put the electrolytic solution (master solution) after cooling down into the liquid bucket, continuously again add the secondary distilled water or de-ionized water, but it can neither exceed the upper limit water level line nor be lower than the low limit water level line. Screw the outer cover tightly and use it after ten minutes.
3.2 Self checking of instrument (Never connect with gas chromatograph)
3.2.1 Connect with the power supply.
3.2.2 Switch on the power supply.
The moment the pressure meter goes up. Verify that the electrolytic indicating lamp (green lamp) on the instrumental panel is lit, digital flow indication (Digital meter) should be more than 300 and less than 350. The pressure indication (Pressure meter) in five minutes should reach up to 4Kg/cm2 (about 0.4Mpa) and digital flow indication drops to “000”. That shows the instrument working in a normal case and the self-checking is qualified.3.3 Operation of instrument (Connect with the gas chromatograph)
3.3.1 Take off the sealing nut located at the outlet port of the rear of the hydrogen generator.
(Please keep it well for the next usage after taking it off).
The outlet port of the hydrogen generator qualified after the self-checking is connected to the inlet port of the hydrogen of the gas chromatograph using a gas tube with the outer diameter of 3mm. Screw up the nut to be sure for good seal. Switch on the power supply and instrument enters into the working status.
3.3.2 Great attention should be taken that the flow display should be in accord with the flow display used by the gas chromatograph. When the flow displayed exceeds more than the actual flow used, promptly stop the instrument running and verify the gas leakage carefully. Please refer to the sections of troubleshooting in this manual. After so, the self-checking is made again. It can be operated until the self-checking of the instrument is qualified
3.3.3 Two steps can be selectable according to user’s requirements. When using the hydrogen as the carrier gas, such as TCD, set the pressure to “H” status for obtaining stable flow and sufficient pressure. When using the hydrogen as the combustion gas, such as FID, set the pressure to “L” status. It not only makes the hydrogen pressure and flow being stable, but also extends the lifetime of the instrument.
Note: Pressure selection is set inside of the instrument. Open the outer cover of the instrument, there is a moveable switch located beside pressure controller between two filters. The user can select it freely according to the different requirements. “H” status is set to 6Kg/cm2 (about 0.6MPa). “L” status is set to 4Kg/cm2 (about 0.4MPa ).
The pressure is set to “L” status when the instrument is delivered.
3.3.4 There are two filters filled in color changing silica gel and molecular sieve provided with the instrument. Observe through the viewed window if the color of the silica gel in the filter has
been changed. If it is so, please immediately make the replacement or regeneration. Its method shows as follows: Rotate off the filter and loose the top cover of the filter. Again screw it tightly after replacing the silica. Mount the filter to the chassis and rotate it tightly. After so, check if the gas leakage exists.
3.3.5 The electrolytic solution is gradually reduced when the instrument is used for a certain period. Therefore add the secondary distilled water or de-ionized water promptly when the electrolytic solution is nearly to low limit. Don’t exceed the water level line of the upper limit when the water is added. The electrolytic solution should be replaced after a half year. (The concentration of the potassium hydroxide used for the hydrogen generator is 10% more or less).
3.3.6 The hydrogen generator can be never run when the pressure shows “0”, otherwise the whole instrument will be worthless.
3.3.7 Don’t detach and open the electrolytic cell by user so as to avoid the instrument running in abnormal case. It can’t be repaired by user self.
3.3.8 Clean up the electrolytic solution in the liquid bucket using an ear ball if the transportation is required. CAUTION: The electrolytic solution of the instrument is like barrel-shaped, a partial electrolytic solution is stocked in the electrolytic cell, therefore, the instrument should be backward 90 degree of tilt even after sucking all of the electrolytic solution in the liquid bucket. The moment the electrolytic solution in the electrolytic cell will flow to the liquid bucket, then again use the ear ball to clean up the electrolytic solution in the liquid bucket. Afterwards screw up the outer cover again when the inner cover is mounted to avoid residual electrolytic solution splitting out during the transportation.
4. WORKING PRINCIPLE AND FEATURES OF INSTRUMENT
4.1 Working principle:
The electrolytic method is utilized to produce the hydrogen. The water solution of potassium hydroxide acts as the electrolytic solution. The noble metal acts as the electrode. The latest filter separation technology is used to wholly separate the hydrogen and oxygen. The transient metal catalytic technology is adopted in the electrolytic cell to make the purity of the hydrogen production contenting oxygen less 3PPM.
The program control used in the instrument adopts high sensitivity, fuzzy control automatic tracking system without using the stable valve and realizes auto-constant voltage and current. The pressure stable precision range will be less 0.001MPa. Amount of the hydrogen required by the gas chromatograph can be automatically adjusted in the range of 0-300ml/min. The hydrogen production will automatically stop when stopping using the hydrogen.
4.2 Features of instrument
4.2.1 Program control:
The specialized chip is used in the control system of the instrument. All working process of the instrument will be completed by the program control. The automatic constant voltage, constant current and hydrogen flow can be automatically adjusted in the range of 0-300ml/min according to the requirements.4.2.2 Operating mode:
There are two working modes selectable: high and low pressures. It is flexible to use it. It not only makes the pressure and flow of the hydrogen stable, as well extends the lifetime of instrument.4.2.3 Low humidity of hydrogen production:
The film separating technique and effective de-humidity device are used in the system, so the original humidity is more reduced. The multi-polar absorption is adopted to make the hydrogen humidity reaching up to -56℃ of dew point temperature..4.2.4 Easy operation:
Only switch on the power supply if the hydrogen is required. It can be used continuously or at intervals, the hydrogen production is very stable without the attenuation.4.2.5 Safe and reliable:
The safe device is equipped with the system, sensitive and reliable.5. TROUBLING SHOOTING
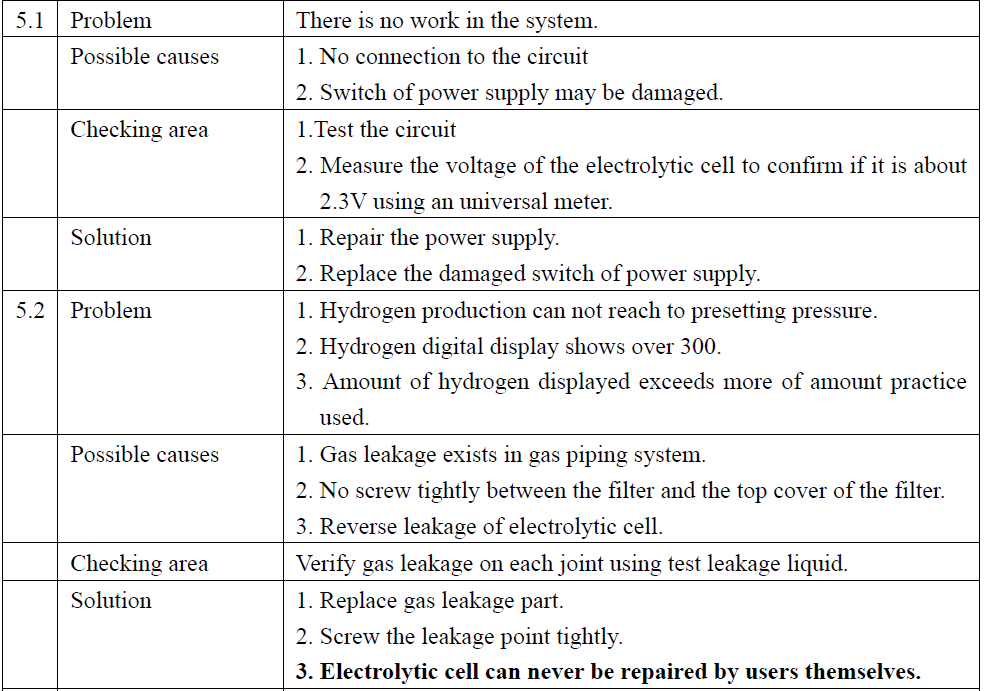
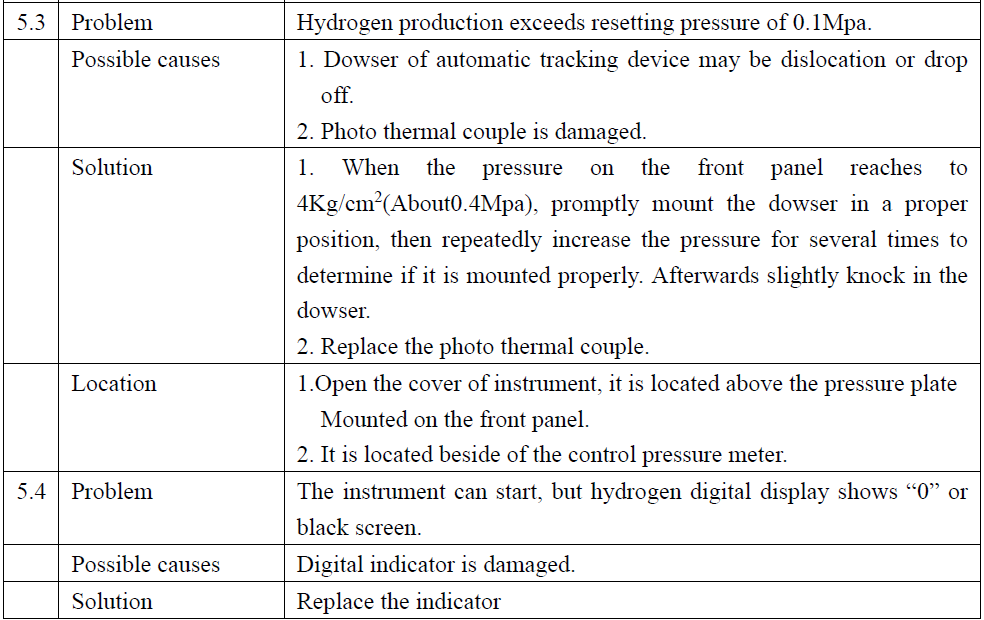
6. MAIN TECHNICAL PARAMETERS
6.1 Hydrogen purity: 99.999% Oxygen content<3PPM, Water content dew point -56℃6.2 Hydrogen flow: 0-300ml/min
6.3 Output pressure: 0-4Kg/cm2 (about 0.4Mpa) (Two steps are adjustable)
0-6Kg/cm2 (about 0.6Mpa)
6.4 Pressure stability: < 0.001MPa
6.5 Power supply: 220V±10%, 50HZ
6.6 Consumption power: 150W
6.7 Ambient temperature: 1-40℃
6.8 Relative humidity: < 85%
6.9 Outer dimension: 370×330×180mm
6.10. Net weight: About 10Kg.
7. Packing list
7.1 BGEN-303 Fully Automatic Hydrogen Generator 1Set7.2 Spare parts:
7.2.1 Ear ball (with ф4 stainless steel tube) 1Kit
7.2.2 Potassium hydroxide (analytical purity) 200g/bottle
7.2.3 Sealing washer of filter (ф14×2.4) 2 Pcs.
7.2.4 Sealing washer of filter (ф26×2.4) 2 Pcs.
7.2.5 Sealing washer of filter (ф32×2.4) 2 Pcs.
7.2.6 Sealing washer of gas piping (Ф6×5) 5 Pcs.
7.2.7 Screw nut (M8×1) 1Pcs.
7.3 Operating manual 1copy